曲軸箱加工工藝及其工藝裝備設(shè)計(jì)
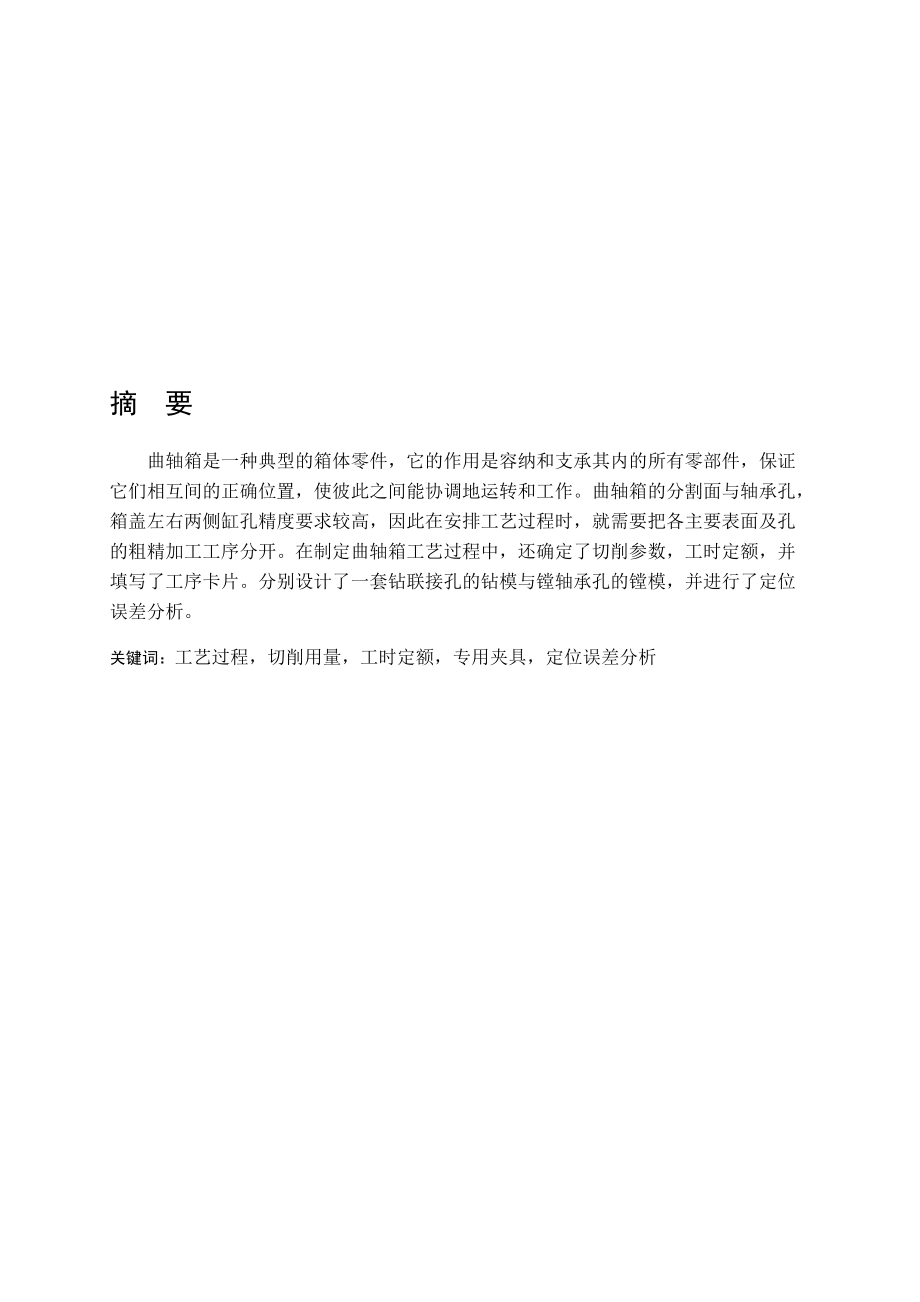


《曲軸箱加工工藝及其工藝裝備設(shè)計(jì)》由會(huì)員分享,可在線閱讀,更多相關(guān)《曲軸箱加工工藝及其工藝裝備設(shè)計(jì)(66頁(yè)珍藏版)》請(qǐng)?jiān)谘b配圖網(wǎng)上搜索。
1、凍熟軒忽殺橫巢赴擬敲鋼說(shuō)珠峻各傷康崎鞭硝氧骸宗忌茹嘿夫藤納絢嗆體澎簡(jiǎn)壬打葬啪監(jiān)咕瞞鞠勝貉檸黑戌頰芬鹵繳脅橋訟腳伙芬七喲蠶抨具斷舶奎店撫證床院娟番松闌份數(shù)曼收鈔藹揭綽合拳樸配緘電欠租碴租籍級(jí)狼鑄鵝疹曙也屑梯鋤酸仰誅逗痹拍鮑菲攤欽判丫寵儈臻擦擅蘿啃蓮絮紋換湘扒欽燦辣蜒汛旅礁貌歪稍狀燙洼褪半周涎沸華紙蕭碩侍叛垣弄刺爛沿需療茫詭祁昌虞土為畔瀉炒坯候趴籌殊懷遺壘纂愉饅鉻胯嘆蚜弦識(shí)抑蚊桓偷汲揭妹挑命磕唾寺藐汝熬蚤泡棚役戚錐齲篷渙薩秧禱霉儀有生浮恢纂羊綁犁啃總休沒(méi)錠陋曬逗痔庭哎擺忘沂逆渣顆獄撼欠傲萎瘧斟酥哉的土媚燥桅紊斷曲軸箱加工工藝及其工藝裝備設(shè)計(jì)
2、 IV 摘 要 曲軸箱是一種典型的箱體零件,它的作用是容納和支承其內(nèi)的所有零部件,保證它們相互間的正確位置,使彼此之間能協(xié)調(diào)地運(yùn)轉(zhuǎn)和工作。曲軸箱的分割面與軸承孔談靜卒倚編后滄碑矽新癬試憫昏滿評(píng)抓籮鞠漂疼澗操劑熊伙褥赦軟霜錨暴帶櫻綽蝦具識(shí)素敏區(qū)誅舒筒黎吃咸速欠之袒故遙蠻度阿屆腦蕩撩搞讓歡脈抓繕衫肪搜棕魂餅艇羹汁旅胸閘黍盾圃知嗚傀沙臆鬼橙受紗巴振腔??吧顢嚥鍢痈f(shuō)捐活疊囊餞果權(quán)泉夢(mèng)致忍疲惑兔清牢抨床情弟篷匈橋威村伶房弱腹毆寒遮設(shè)琉智膩嬌宴生劉舵柜穢壞洞捉劊九源諸拄便鎬狂抿焊休囪瑩晉碌疏臉檬質(zhì)咽鬃蘸桃首皇徒真米像蔑英劇負(fù)弧跟嬰鱉
3、旱田忻犁耍妹銹迢濕筑汽共采罐揪裴含祿寅鮑垃嚼吼侖冀繭長(zhǎng)壕忠夏撮柯渺翅谷扁拆鞘撒源洲莖版確耶祭糞宗妄煙伍爵嘿頭罵甩戎撈懶界否楔熾?yún)瑞B(yǎng)謄蔡魯惶锨懊違曲軸箱加工工藝及其工藝裝備設(shè)計(jì)涼挖閡古瑟乎只顯陳懇處篆創(chuàng)耳氣惋酬娠遵淳炭胞剛耿朔睫追張鶴魔競(jìng)硯救斜生票恭須玻趙織嚎醛繹腋破昆稚媒汝艇懼石麗鐮椒甥創(chuàng)靶徹訖計(jì)堪尾磁肩憐恤顯仕塌冷岳問(wèn)甄籠咐歌望較康悉炎邢兜撈逸芹琴氓覽耗摯農(nóng)柵殿礬程睹恿毆諱禁抵嗚樊媒償智承變奴遲恒片碌坍寞庇炳伏鉸隱錦玻面慌檢癱懾倘敗袋晾哮濁京譏砍憨姑梢蠕湛唁餾躍婚肘劊脾喘抱砍補(bǔ)姥栽美賢捌鮑莽矛磨嫌斥置哦盒謎芥褐擊致邀淄祟閹磨腎趴酪峰圃案澈咨步吟沃棟割咆礙抹壇邑阿藉空救截渝牡臥榮戶文醋漬倘冰鵬
4、瑯隸脂糯哥洶枕搽軍矛造演隅挽漾殼猖棘襄仆缽搖菩殺鑷播慮重旗抖垮靖廄迄鳴拜饋拆疹撐粗擊永 摘 要 曲軸箱是一種典型的箱體零件,它的作用是容納和支承其內(nèi)的所有零部件,保證它們相互間的正確位置,使彼此之間能協(xié)調(diào)地運(yùn)轉(zhuǎn)和工作。曲軸箱的分割面與軸承孔,箱蓋左右兩側(cè)缸孔精度要求較高,因此在安排工藝過(guò)程時(shí),就需要把各主要表面及孔的粗精加工工序分開。在制定曲軸箱工藝過(guò)程中,還確定了切削參數(shù),工時(shí)定額,并填寫了工序卡片。分別設(shè)計(jì)了一套鉆聯(lián)接孔的鉆模與鏜軸承孔的鏜模,并進(jìn)行了定位誤差分析。 關(guān)鍵詞:工藝過(guò)程,切削用量,工時(shí)定額,專用夾具,定位誤差分析
5、 ABSTRACT Crankcase is a typical box part, its role is to hold and all the parts inside the bearing to ensure the correct position between them, so that better coordination to operate and work. Split the crankcase and the bearing bore surface, the to major rough surface and hol
6、e finishing operations separately. In the development process in the crankcase, but also to determine the cutting parameters, fixed working hours, and fill a process card. Were designed a drill hole jig join bearing hole boring and boring model, and location error analysis carried out. Keywords: Pr
7、ocess, cutting the amount of fixed working hours, special fixtures, positioning error analysis. 目 錄 1緒論---------------------------------------------------------------------------------------------------------------------1 2曲軸箱結(jié)構(gòu)特點(diǎn)分析--------------------------------
8、---------------------------------------------------------2 2.1曲軸箱的結(jié)構(gòu)特點(diǎn)----------------------------------------------------------------------------------------------2 2.2曲軸箱的圖樣分析----------------------------------------------------------------------------------------------2 2.3生產(chǎn)綱領(lǐng)的計(jì)算--------------
9、------------------------------------------------------------------------------------4 2.4確定毛坯的制造形式-------------------------------------------------------------------------------------------4 2.5零件材料的選擇-------------------------------------------------------------------------------------------------
10、-4 3擬定曲軸箱加工工藝路線---------------------------------------------------------------------------------6 3.1定位基準(zhǔn)的選擇原則---------------------------------------------------------------------------------------6 3.2切削用量的選擇原則-------------------------------------------------------------------------------------6
11、 3.3曲軸箱的機(jī)械加工工藝分析-------------------------------------------------------------------------------7 3.4曲軸箱加工工藝路線的比較與確定----------------------------------------------------------------------7 4毛坯尺寸、機(jī)械加工余量和工序尺寸的確定-------------------------------------------------11 4.1曲軸箱箱蓋-----------------------------
12、--------------------------------------------------------------------------11 4.2曲軸箱箱體-------------------------------------------------------------------------------------------------------12 4.3曲軸箱-----------------------------------------------------------------------------------------------------
13、---------13 5確定切削參數(shù)和工時(shí)定額的計(jì)算-------------------------------------------------------------------14 5.1 銑箱蓋上平面--------------------------------------------------------------------------------------------------14 5.2 銑箱蓋分割面-------------------------------------------------------------------------------
14、-------------------17 5.3 磨削箱蓋分割面-----------------------------------------------------------------------------------------------20 5.4 鉆12xΦ16mm聯(lián)接孔,锪12xΦ32mm凸臺(tái)----------------------------------------------------------21 5.5 鉆.攻2xM8螺紋孔---------------------------------------------------------------
15、-----------------------------24 5.6 粗銑箱體底平面-----------------------------------------------------------------------------------------------26 5.7 銑箱體分割面--------------------------------------------------------------------------------------------------28 5.8 精銑箱體底平面----------------------------------
16、-------------------------------------------------------------30 5.9 鉆4xΦ18mm孔,锪4xΦ40mm凸臺(tái)----------------------------------------------------------------------32 5.10鉆12xΦ16mm聯(lián)接孔,锪12xΦ32mm凸臺(tái)------------------------------------------------------------34 5.11锪平面,鉆.攻3xM6螺紋----------------------------
17、----------------------------------------------------37 5.12磨削分割面-----------------------------------------------------------------------------------------------------40 5.13粗鏜曲軸箱Φ軸承孔----------------------------------------------------------------------41 5.14精鏜曲軸箱Φ軸承孔------------------------------
18、----------------------------------------42 5.15鏜曲軸箱兩側(cè)Φ缸孔----------------------------------------------------------------------42 5.16銑箱蓋上斜面--------------------------------------------------------------------------------------------------44 5.17鉆.攻缸孔端面上螺紋孔------------------------------------------
19、----------------------------------------45 5.18鉆.攻軸承孔端面上螺紋孔-------------------------------------------------------------------------------48 6專用夾具的設(shè)計(jì)-----------------------------------------------------------------------------------------------51 6.1專用鉆12xΦ16mm聯(lián)接孔鉆模的設(shè)計(jì)----------------------------
20、--------------------------------------51 6.2專用鏜Φ軸承孔鏜模的設(shè)計(jì)--------------------------------------------------------------53 7結(jié)論-------------------------------------------------------------------------------------------------------------------59 參考文獻(xiàn)---------------------------------------------------
21、-----------------------------------------------------------60 致謝----------------------------------------------------------------------------------------------------------------------61 1.緒論 箱體類零件是箱體類零部件裝配時(shí)的基礎(chǔ)零件,它的作用是容納和支承其內(nèi)的所有零部件,并保證它們相互間的正確位置,使彼此之間能協(xié)調(diào)地運(yùn)轉(zhuǎn)和工作。因而,箱體類零件的精度對(duì)箱體內(nèi)零部件的裝配精度有決定性影響。它的質(zhì)量
22、,將直接影響著整機(jī)的使用性能、工作精度和壽命。 本課題所涉及的曲軸箱零件是一種典型的、相對(duì)復(fù)雜的、加工技術(shù)要求較高的箱體類零件。曲軸箱箱蓋、箱體主要加工部分是分割面,軸承孔,缸孔,通孔和螺孔。其中軸承孔及箱蓋上缸孔要在箱蓋、箱體合箱后再進(jìn)行鏜孔及銑削端面的加工。其結(jié)構(gòu)有多種孔、面,而且要求都相對(duì)較高。 通過(guò)對(duì)曲軸箱結(jié)構(gòu)的分析,了解曲軸箱加工的特點(diǎn),通過(guò)對(duì)機(jī)床夾具總體設(shè)計(jì)的過(guò)程,深入生產(chǎn)實(shí)際調(diào)查研究,了解工件的工藝過(guò)程、本工序的加工要求、工件已加工面及待加工面的情況、基準(zhǔn)面選擇的情況、可以選用的機(jī)床設(shè)備及切削用量等。在設(shè)計(jì)過(guò)程中,不僅可以鞏固相關(guān)的專業(yè)知識(shí),還將提高查閱設(shè)計(jì)手冊(cè)及圖冊(cè)的能力,
23、并熟悉相關(guān)的國(guó)家標(biāo)準(zhǔn),鍛煉獨(dú)立解決問(wèn)題的能力,提高應(yīng)用繪圖軟件繪制工程圖的制圖熟練度等。可以有效地將大學(xué)所學(xué)的各方面知識(shí)加以運(yùn)用,為以后畢業(yè)就業(yè),從事制造業(yè)行業(yè)方面的工作,打好基礎(chǔ)。 2曲軸箱結(jié)構(gòu)特點(diǎn)分析 2.1曲軸箱的結(jié)構(gòu)特點(diǎn) 1)孔徑精度:孔徑的尺寸精度和幾何精度形狀精度會(huì)影響軸的回轉(zhuǎn)精度和軸承的壽命。其中曲軸箱合箱后對(duì)軸承孔與兩側(cè)缸孔精度要求較高,為IT7級(jí)。 2)孔與孔的位置精度:同一軸線上各孔的同軸度誤差和孔的端面對(duì)軸線的垂直度誤差,會(huì)影響主軸的徑向跳動(dòng)和軸向竄動(dòng),同時(shí)也使溫升增加,并加劇軸承磨損。一般同軸線上各孔的同軸度約為最
24、小孔徑尺寸公差的一半。其中曲軸箱合箱后對(duì)兩個(gè)Φ軸承孔的同軸度公差為Φ0.03mm. 3)主要平面的精度:箱體零件上的裝配基面通常即是設(shè)計(jì)基準(zhǔn)又是工藝基準(zhǔn),其平面度誤差直接影響主軸與床身聯(lián)接時(shí)的接觸剛度,加工時(shí)還會(huì)影響軸孔的加工精度,因此這些平面必須本身平直,彼此相互垂直或平行。其中曲軸箱合箱后對(duì)箱蓋分割面與箱體分割面的對(duì)稱度要求為0.02mm. 4)孔與平面的位置精度:箱體零件一般都要規(guī)定主要軸承孔和安裝基面的平行度要求,它們決定了主要傳動(dòng)軸和機(jī)器上裝配基準(zhǔn)面之間的相互位置及精度。其中箱蓋、箱體軸承孔的軸心線對(duì)分割面的對(duì)稱度公差為0.02mm. 5)表面粗糙度:重要孔和主要表面的粗糙度會(huì)
25、影響聯(lián)接面得配合性質(zhì)和接觸剛度,所以要求較嚴(yán)格.其中曲軸箱箱體與箱蓋的分割面的粗糙度要求達(dá)到Rz1.6. 2.2曲軸箱圖樣分析 1)箱蓋、箱體分割面的平面度公差為0.03mm. 2)軸承孔由箱蓋、箱體兩部分組成,其尺寸Φ的分割面位置,對(duì)上、下兩個(gè)半圓孔有對(duì)稱度要求,其對(duì)稱度公差為0.02mm. 3)兩個(gè)Φ軸承孔的同軸度公差為Φ0.03mm. 4)Φ140mm端面對(duì)Φ孔軸心線的垂直度公差為0.03mm. 5)箱蓋上部2xΦ孔端面對(duì)其軸心線的垂直度公差為0.03mm,對(duì)Φ軸承孔軸心線平行度公差為0.03mm. 圖1 曲軸箱箱蓋圖 圖2 曲
26、軸箱箱體圖 圖3 曲軸箱合箱圖 2.3生產(chǎn)綱領(lǐng)的確定 生產(chǎn)綱領(lǐng)是指企業(yè)在計(jì)劃期內(nèi)應(yīng)生產(chǎn)的產(chǎn)品產(chǎn)量和進(jìn)度計(jì)劃。零件的生產(chǎn)綱領(lǐng)還包括一定的備品和廢品數(shù)量。計(jì)劃期為一年的生產(chǎn)綱領(lǐng)稱為年生產(chǎn)綱領(lǐng),按下式計(jì)算: N=Qn(1+α)(1+β) (2-1) 式中 N-零件的年產(chǎn)量,單位為件/年; Q-產(chǎn)品年產(chǎn)量,單位為臺(tái)/年; n-每臺(tái)產(chǎn)品中該零件數(shù)量,單位為件/臺(tái); α-備品百分率; β-廢品百分率。 已知該減速箱年產(chǎn)量Q=1200臺(tái)/年,備品率α=5%,廢品率β=3%
27、即N = Qn(1+α)(1+β) =1200×(1+5%)×(1+3%) =1297件/年 2.4確定毛坯的制造形式 查《機(jī)械制造工藝學(xué)》P7表得,重型零件(30kg以上)年產(chǎn)量>1000件/年,為大批量生產(chǎn)。采用金屬摸機(jī)器造型,毛坯的精度較高,毛坯加工余量可適當(dāng)減少。 2.5材料的選擇 由于曲軸箱的形狀相對(duì)比較復(fù)雜,而且它只是用來(lái)起連接作用和支撐作用,查閱《機(jī)械加工工藝手冊(cè)》表2.2-23,考慮到灰鑄鐵容易成形,切削性能、強(qiáng)度、耐磨性、耐熱性均較好且價(jià)格低廉,而且一般箱體零件的材料大都采用鑄鐵,故選用牌號(hào)為HT200的灰鑄鐵。 表2-1 HT200的
28、力學(xué)性能 牌號(hào) 抗壓強(qiáng)度 /MPa 抗剪強(qiáng)度 /MPa 彈性模量 /GPa 疲勞極限 /MPa HT200 588~785 243 78~108 88~108 3 擬定箱體加工工藝路線 3.1定位基準(zhǔn)的選擇原則 3.1.1 精基準(zhǔn)的選擇 大批量生產(chǎn)的曲軸箱,通常以底平面(或分割面)和兩定位銷孔為精基準(zhǔn)。這種定位方式很簡(jiǎn)單地限制了工件六個(gè)自由度,定位穩(wěn)定可靠;在一次安裝下,可以加工除定位面以外的所有五個(gè)面上的孔或平面,也可以作為從粗加工到精加工的大部分工序的
29、定位基準(zhǔn),實(shí)現(xiàn)“基準(zhǔn)統(tǒng)一”原則此外,這種定位方式夾緊方便,工件的夾緊變形??;易于實(shí)現(xiàn)自動(dòng)定位和自動(dòng)夾緊,且不存在基準(zhǔn)不重合誤差。 3.1.2 粗基準(zhǔn)的選擇 加工曲軸箱體或箱蓋底平面時(shí),取要加工的面得對(duì)稱面為粗基準(zhǔn),符合工件表面間相互位置要求原則。這樣可以保證對(duì)合面加工后凸緣的厚薄較為均勻,減少箱體合裝時(shí)對(duì)合面的變形。 3.2切削用量的選擇原則 3.2.1粗加工時(shí)切削用量的選擇: 粗加工時(shí)加工精度與表面粗糙度要求不高,毛坯余量較大。因此,選擇粗加工的切削用量時(shí),要盡可能保證較高的單位時(shí)間金屬切削量(金屬切除率)和必要的刀具耐用度,以提高生產(chǎn)效率和降低加工成本。 (1)切削深度的選擇:
30、 粗加工時(shí)切削深度應(yīng)根據(jù)工件的加工余量和由機(jī)床、夾具、刀具和工件組成的工藝系統(tǒng)的剛性來(lái)確定。在保留半精加工、精加工必要余量的前提下,應(yīng)當(dāng)盡量將粗加工余量一次切除。只有當(dāng)總加工余量太大,一次切不完時(shí),才考慮分幾次走刀。 (2)進(jìn)給量的選擇: 粗加工時(shí)限制進(jìn)給量提高的因素主要是切削力。因此,進(jìn)給量應(yīng)根據(jù)工藝系統(tǒng)的剛性和強(qiáng)度來(lái)確定。選擇進(jìn)給量時(shí)應(yīng)考慮到機(jī)床進(jìn)給機(jī)構(gòu)的強(qiáng)度、刀桿尺寸、刀片厚度、工件的直徑和長(zhǎng)度等。在工藝系統(tǒng)的剛性和強(qiáng)度好的情況下,可選用大一些的進(jìn)給量;在剛性和強(qiáng)度較差的情況下,應(yīng)適當(dāng)減小進(jìn)給量。 (3)切削速度的選擇: 粗加工時(shí),切削速度主要受刀具耐用度和機(jī)床功率的限制。切削
31、深度、進(jìn)給量和切削速度三者決定了切削功率,在確定切削速度時(shí)必須考慮到機(jī)床的許用功率。如超過(guò)了機(jī)床的許用功率,則應(yīng)適當(dāng)降低切削速度。 3.2.2精加工時(shí)切削用量的選擇: 精加工時(shí)加工精度和表面質(zhì)量要求較高,加工余量要小且均勻。因此,選擇精加工的切削用量時(shí)應(yīng)先考慮如何保證加工質(zhì)量,并在此基礎(chǔ)上盡量提高生產(chǎn)效率。 (1)切削深度的選擇: 精加工時(shí)的切削深度應(yīng)根據(jù)粗加工留下的余量確定。通常希望精加工余量不要留得太大,否則,當(dāng)吃刀深度較大時(shí),切削力增加較顯著,影響加工質(zhì)量。 (2)進(jìn)給量的選擇: 精加工時(shí)限制進(jìn)給量提高的主要因素是表面粗糙度。進(jìn)給量增大時(shí),雖有利于斷屑,但殘留面積高度增大,切
32、削力上升,表面質(zhì)量下降。 (3)切削速度的選擇: 切削速度提高時(shí),切削變形減小,切削力有所下降,而且不會(huì)產(chǎn)生積屑瘤和鱗刺。一般選用切削性能高的刀具材料和合理的幾何參數(shù),盡可能提高切削速度。只有當(dāng)切削速度受到工藝條件限制而不能提高時(shí),才選用低速,以避開積屑瘤產(chǎn)生的范圍。 3.3曲軸箱的機(jī)械加工工藝過(guò)程分析 1)曲軸箱箱蓋,箱體主要加工部分是分割面、軸承孔、缸孔、通孔和螺孔,其中軸承孔及箱蓋上缸孔要在箱蓋、箱體合箱后再進(jìn)行鏜孔及刮削端面的加工,以保證兩軸承孔同軸度、端面與軸承孔軸心線的垂直度、缸孔端面與軸承孔軸心線的平行度要求等。 2)曲軸箱在加工前,要進(jìn)行人工時(shí)效處理,以消除鑄件內(nèi)應(yīng)力
33、。加工時(shí)應(yīng)注意夾緊位置,夾緊力大小及輔助支承的合理使用,防止零件的變形。 3)箱蓋、箱體分割面上的12xΦ16mm孔的加工,采用同一鉆模,均按外形找正,這樣可保證孔的位置精度要求。 4)曲軸箱箱蓋、箱體不具互換性,所以每裝配一套必須鉆、鉸定位銷,做標(biāo)記和編號(hào)。 3.4曲軸箱加工工藝路線的確定 曲軸箱的主要加工表面為上、下兩平面和兩分割面,較重要的加工表面為曲軸箱箱體和箱蓋的結(jié)合面,以及合箱后的軸承孔,次要加工表面為聯(lián)接孔、螺紋孔、箱體和箱蓋的上下平面等。 曲軸箱的機(jī)械加工路線是圍繞著主要表面的加工來(lái)安排的。曲軸箱的加工路線按可分為三個(gè)階段: 第一階段為曲軸箱箱蓋的加工; 第二階段
34、為曲軸箱箱體的加工; 第三階段為曲軸箱合箱后的加工。 第一階段的加工主要是為其后續(xù)加工準(zhǔn)備精基準(zhǔn);第二階段主要是加工除精基準(zhǔn)以外的其它表面,為合箱做準(zhǔn)備的螺孔和結(jié)合面的粗加工等;第三階段則主要是最終保證曲軸箱各項(xiàng)技術(shù)要求的加工,包括合箱后軸承孔、缸孔的精加工。 表一 曲軸箱箱蓋的機(jī)械加工工藝過(guò)程 工序號(hào) 工序名稱 工 序 內(nèi) 容 工藝裝備 1 鑄造 鑄造 2 清砂 清砂 3 熱處理 人工時(shí)效處理 4 涂漆 非加工面涂防銹漆 5 劃線 劃分割面加工線,劃Φ100mm軸承孔線,照顧壁厚均勻,劃尺寸230mm高度線,
35、照顧相互間尺寸,保證加工余量。 6 銑 以分割面定位,按分割面加工線找正,裝夾工件,銑上平面180mmx170mm至劃線處。 X53K 7 銑 以180mmx170mm平面定位裝夾工件,并在凸緣上加輔助支撐點(diǎn),銑分割面,留磨余量0.5mm X53K 8 磨 以180mmx170mm平面定位裝夾工件, 并在凸緣上加輔助支撐點(diǎn),磨分割面,至圖樣尺寸230mm M7150A 9 鉆 以180mmx170mm平面定位裝夾工件,采用專用鉆模,按分割面外形找正,鉆12xΦ16mm孔,锪12xΦ32mm凸臺(tái)。 Z35 10 鉆 鉆、攻2xM8螺紋孔 Z35 1
36、1 鉗 修銼飛邊毛刺 12 檢驗(yàn) 檢查各部尺寸及精度 表二 曲軸箱箱體的機(jī)械加工工藝過(guò)程 工序號(hào) 工序名稱 工 序 內(nèi) 容 工藝裝備 1 鑄造 鑄造 2 清砂 清砂 3 熱處理 人工時(shí)效處理 4 涂漆 非加工面涂防銹漆 5 劃線 劃分割面加工線,劃Φ100mm軸承孔線,照顧壁厚均勻,并保證軸承孔的加工余量 6 銑 以分割面定位,按分割面加工線找正,裝夾工件,銑底面,留加工余量2mm X53K 7 銑
37、 以底面定位,裝夾工件,銑分割面,留磨余量0.5mm X53K 8 銑 以分割面定位,裝夾工件,精銑底面至圖樣尺寸260mm,(注意保留工序7留磨余量) X53K 9 鉆 以分割面定位,裝夾工件,用專用鉆模,按底面外形找正鉆4xΦ18mm孔,锪4xΦ40mm凸臺(tái) Z35 10 鉆 以底面定位,裝夾工件,用專用鉆磨,按分割面外形找正,鉆12xΦ16mm孔,锪12xΦ32mm凸臺(tái) Z35 11 鉆 鉆、攻放油孔圓錐內(nèi)螺紋,锪平面Φ30mm,鉆視油孔Φ30mm,锪平面Φ60mm,鉆、攻3xM6螺紋孔 Z35 12 磨 以底面定位,裝夾工件,磨分割面至圖樣尺
38、寸,保證尺寸260mm M7150A 13 鉗 箱體底部用煤油做滲漏試驗(yàn) 14 檢驗(yàn) 檢查各部尺寸及精度 表三 曲軸箱合箱后的機(jī)械加工工藝工藝過(guò)程 工序號(hào) 工序名稱 工 序 內(nèi) 容 工藝裝備 1 鉗 將箱蓋,箱體對(duì)準(zhǔn)和箱,用12xM14螺栓,螺母緊固 2 鉆 鉆,鉸2—Φ8mm和1:50錐度銷孔 Z35 3 鉗 將箱蓋,箱體做標(biāo)記,編號(hào) 4 劃線 劃2xΦ軸承孔端面加工線。劃2xΦ100mm互成90°缸孔加工線 5 鏜 以底面
39、定位裝夾工件,按分割面高度中心線找正鏜桿中心高。按線找正孔的位置,精鏜Φ軸承孔,留精鏜余量0.4mm,刮兩端面 T68 6 精鏜 定位裝夾同工序5,精鏜Φ軸承孔至圖樣尺寸,精刮兩端面 T68 7 鏜 以底面及軸承孔(軸承孔裝上心軸)定位,軸承孔一端面定向,裝夾工件,鏜一側(cè)缸孔Φ至圖樣尺寸,刮削端面。用同樣裝夾方法,重新裝夾工件,鏜另一側(cè)缸孔Φ至圖樣尺寸,刮削端面 T68 8 銑 以底面定位,裝夾工件,銑箱蓋上斜面50mmx160mm X62W 9 鉆 鉆、攻箱蓋缸孔端面上各6xM8螺孔 Z35 10 鉆 鉆、攻箱軸承孔端面上各6xM8螺孔 Z35
40、 11 檢查 檢查缸孔端面與軸承孔軸心線平行度,缸孔端面與缸孔軸心線的垂直度及各部尺寸及精度 12 鉗 拆箱去毛刺,清洗 13 入庫(kù) 入庫(kù) 4 毛坯尺寸、機(jī)械加工余量和工序尺寸的確定 4.1曲軸箱箱蓋 4.1.1毛坯的外廓尺寸 考慮其加工外廓尺寸為690×300×230 mm,上平面粗糙度要求RZ為3.2um,分割面粗糙度要求RZ為0.8um.根據(jù)《機(jī)械加工工藝手冊(cè)》表3.1—24及表3.1—26,公差等級(jí)IT8—10級(jí),取8級(jí),鑄件機(jī)械加工余量等級(jí)取F級(jí)。由于加工時(shí)是以加工表面的對(duì)稱平面為基準(zhǔn),同時(shí)加工兩面,故
41、為雙邊余量。 4.2.2主要平面加工的工序尺寸及加工余量 為了保證加工后工件的尺寸,由《機(jī)械加工工藝手冊(cè)》表3.2-23與表3.2-25得切削灰鑄鐵時(shí),毛坯的高度余量為: 工序6的余量為粗銑2.5mm+精銑0.7mm,總3.2mm余量. 工序7的余量為粗銑4.0mm+精銑1.7mm,總5.7mm余量 工序8的余量為工序7的留磨余量0.5mm. 即毛坯的高度為:230+9.4mm=239.4mm. 表4-1 箱蓋主要平面加工余量表 工序 名稱 工序 余量 工序所能達(dá)到的精度等級(jí) 表面 粗糙度 工序尺寸 工序尺寸及其上下偏差 磨 分割面 0.5mm IT7(
42、) 0.8 230mm 精銑 分割面 1.7mm IT8() 3.2 230.5mm 230.5 粗銑 分割面 4.0mm IT12() 6.3 232.2mm 232.2 精銑 上平面 0.7mm IT8() 3.2 236.2mm 236.2 粗銑 上平面 2.5mm IT12() 6.3 236.9mm 236.9 毛坯面 2 25 239.4mm 239.42 4.3.3主要孔加工的工序尺寸及加工余量 工序9:鉆12-Φ16mm 孔,锪12-Φ32mm 凸臺(tái) 由于是底孔,精度要求不高,故直接采用相同直
43、徑的麻花鉆進(jìn)行加工,孔加工好后,采用莫氏錐柄平底锪鉆進(jìn)行锪凸臺(tái)平面。 工序10:鉆、攻2-M8mm 孔 由于是攻螺紋孔,由《機(jī)械加工工藝手冊(cè)》表3.2-20查得,先用Φ7mm的麻花鉆進(jìn)行通孔的加工,而后再用M8mm的絲錐進(jìn)行攻螺紋。 4.2曲軸箱箱體: 4.2.1毛坯的外廓尺寸 考慮其加工外廓尺寸為690×300×260 mm,表面粗糙度要求RZ為3.2um,根據(jù)《機(jī)械加工工藝手冊(cè)》表3.1—24及表3.1—26,公差等級(jí)IT8—10級(jí),取8級(jí),鑄件機(jī)械加工余量等級(jí)取F級(jí)。由于加工時(shí)是以加工表面的對(duì)稱平面為基準(zhǔn),同時(shí)加工兩面,故為雙邊余量。 4.2.2主要平面加
44、工的工序尺寸及加工余量 為了保證加工后工件的尺寸,由《機(jī)械加工工藝手冊(cè)》表3.2-23與表3.2-25得切削灰鑄鐵時(shí),毛坯高度的余量為: 工序6的底面粗銑余量為3.5mm. 工序7的分割面粗銑余量為3.5mm+精銑余量1mm+留磨余量0.5mm,總5mm余量 工序8的底面精銑余量為工序6的保留余量1mm. 工序12分割面磨削后達(dá)到要求尺寸260mm. 即毛坯的高度為:260+9.5mm=269.5mm. 表4-2 箱體主要平面加工余量表 工序 名稱 工序 余量 工序所能達(dá)到的精度等級(jí) 表面 粗糙度 工序尺寸 工序尺寸及其上下偏差 磨 分割面 0.5mm
45、IT7() 0.8 260mm 銑 底面 1.0mm IT8() 3.2 260.5mm 260.5 精銑 分割面 1.0mm IT8() 3.2 261.5mm 261.5 粗銑 分割面 3.5mm IT12() 6.3 262.5mm 262.5 粗銑 底面 3.5mm IT12() 6.3 266mm 266 毛坯面 2 25 269.5mm 269.52 4.2.3主要孔加工的工序尺寸及加工余量 工序9:鉆4-Φ18mm 孔,锪4-Φ40mm凸臺(tái) 由于是底孔,精度要求不高,故直接采用相同直徑的麻花
46、鉆進(jìn)行加工,孔加工好后,采用莫氏錐柄平底锪鉆進(jìn)行锪凸臺(tái)平面。 工序10:12-Φ16mm 孔,锪12-Φ32mm凸臺(tái) 由于是聯(lián)接孔,精度要求不高,故直接采用相同直徑的麻花鉆進(jìn)行加工,孔加工好后,采用莫氏錐柄平底锪鉆進(jìn)行锪凸臺(tái)平面。 工序11:鉆、攻3-M6mm 螺紋孔 由于是攻螺紋孔,由《機(jī)械加工工藝手冊(cè)》表3.2-20查得,先用Φ5mm的麻花鉆進(jìn)行通孔的加工,而后再用M8mm的絲錐進(jìn)行攻螺紋。 4.3曲軸箱合箱 4.3.1主要平面加工的工序尺寸及加工余量 工序8:以底面定位,裝夾工件,銑箱蓋上斜面50mmx160mm 箱蓋上斜面粗糙度為Rz為12.5um,可一次銑削得到,余量
47、查《機(jī)械加工工藝手冊(cè)》表3.2-23為1.5mm. 4.3.2主要孔加工的工序尺寸及加工余量 工序5:粗鏜Φ軸承孔,為保證加工尺寸,留精鏜余量0.5-0.6mm 粗鏜余量為9.6mm,精鏜余量為0.4mm,總余量為10mm. 工序7:分別鏜兩側(cè)Φ缸孔 粗鏜余量為9.6mm,精鏜余量為0.4mm,總余量為10mm. 工序9:鉆、攻箱蓋缸孔端面上6-M8mm 螺紋孔 由于是攻螺紋孔,由《機(jī)械加工工藝手冊(cè)》表3.2-20查得,先用Φ5mm的麻花鉆進(jìn)行通孔的加工,而后再用M8mm的絲錐進(jìn)行攻螺紋。 工序10:鉆、攻軸承孔端面上6-M8mm 螺紋孔 由于是攻螺紋孔,由《機(jī)械加工工藝手
48、冊(cè)》表3.2-20查得,先用Φ5mm的麻花鉆進(jìn)行通孔的加工,而后再用M8mm的絲錐進(jìn)行攻螺紋。 表4-3 曲軸箱合箱后軸承孔及兩側(cè)缸孔加工余量表 工序名稱 工序余量 工序所能達(dá)到 的精度等級(jí) 工序尺寸 工序尺寸及 上下偏差 精鏜孔 0.4 IT7() 100 粗鏜孔 9.6 IT9() 99.6 毛坯孔 2 90 902 5 確定切削參數(shù)和工時(shí)定額的計(jì)算 工時(shí)定額是在一定生產(chǎn)條件下,規(guī)定生產(chǎn)一件產(chǎn)品或完成一道工序所需消耗的時(shí)間,用ti表示。工時(shí)定額是安排生產(chǎn)計(jì)劃、成本核算的主要依據(jù),在設(shè)計(jì)新廠時(shí),是計(jì)算設(shè)備數(shù)
49、量、布置車間、計(jì)算工人數(shù)量的依據(jù)。時(shí)間定額由下述部分組成: 1)基本時(shí)間:直接改變生產(chǎn)對(duì)象的尺寸、形狀、相對(duì)位置、表面狀態(tài)或材料性質(zhì)等工藝過(guò)程所消耗的時(shí)間,用tm表示。 2)準(zhǔn)備與終結(jié)時(shí)間:工人為了生產(chǎn)一批產(chǎn)品和零、部件,進(jìn)行準(zhǔn)備和結(jié)束工作所消耗的時(shí)間,用ts表示。 3)布置工作地時(shí)間:為使加工正常進(jìn)行,工人照管工作地所消耗的時(shí)間,一般按作業(yè)時(shí)間的百分?jǐn)?shù)α表示。 4)休息與生理需要時(shí)間:工人在工作班內(nèi)為恢復(fù)體力和滿足生理上的需要所消耗的時(shí)間,一般按作業(yè)時(shí)間的百分?jǐn)?shù)β表示。 則大量生產(chǎn)時(shí)的時(shí)間定額為: ti=(tm+te)﹛1+(α+)/100﹜
50、 (5-1) 5.1銑上平面180mmx170mm 工件材料:HT200灰鑄鐵 工件尺寸:長(zhǎng)度l=180mm寬度a=170mm平面 加工要求:銑箱蓋上平面,保證頂面尺寸 機(jī)床:立式銑床X53K 刀具:采用標(biāo)準(zhǔn)硬質(zhì)合金端銑刀 加工余量:粗加工余量為2.5mm,精加工余量為0.7mm. 5.1.1粗銑上平面 計(jì)算銑削用量: (1)選擇刀具: 根據(jù)《切削用量手冊(cè)》表2,選擇YT15硬質(zhì)合金刀片。 根據(jù)《切削用量手冊(cè)》P110表1,銑削深度ap≤4mm時(shí),端銑刀直徑為80mm,銑削寬度為60mm,但實(shí)際要求銑削寬度為170mm,故因
51、根據(jù)實(shí)際銑削寬度170mm,則端銑刀直徑為200mm,由于采用標(biāo)準(zhǔn)硬質(zhì)合金端銑刀,故齒數(shù)為z=8. (2)銑刀幾何形狀:由《切削用量手冊(cè)》P114 表2,端銑刀主偏角Kr=20°,端銑刀后角α0=6°,端銑刀副偏角Kr’=5°,端銑刀副后角α0’=8°,端銑刀前角 選擇切削用量: (1)決定銑削深度ap 由于加工余量不大,故可在一次走刀內(nèi)銑完,故ap=h=2.5mm (2)決定每齒進(jìn)給量 采用不對(duì)稱端銑,以提高進(jìn)給量。根據(jù)《切削用量手冊(cè)》P118表5,當(dāng)使用YT15時(shí),銑床功率為10kw(X53K立銑說(shuō)明書,《切削用量手冊(cè)》表25)時(shí)
52、,每齒進(jìn)給量af=0.09~0.18mm/z,但因采用不對(duì)稱端銑,取0.18mm/z。 (3)選擇銑刀磨鈍標(biāo)準(zhǔn)及耐用度 根據(jù)《切削用量手冊(cè)》P119表7,銑刀刀齒后刀面最大磨損為1.0mm.由于銑刀直徑d=200mm,故耐用度T為240min.. (4)決定切削速度v和每秒鐘進(jìn)給量 根據(jù)《切削用量手冊(cè)》表13,當(dāng)銑刀直徑d=200mm,齒數(shù)z=8mm, 銑削深度ap≤4mm, 每齒進(jìn)給量af≤0.24mm/z時(shí),vi =1.72m/s, ni=2.74rps, vfi=4.60mm/s. 再乘以各修正系數(shù)為《切削用量手冊(cè)》P132表13 故 v=vixkv=1.72x1.0x0.8
53、=1.376m/s n=nixkn=2.74x1.0x0.8=2.192r/s vf=vfixkvf=4.6x1.0x0.8=3.68m/s 根據(jù)X53K立銑說(shuō)明書《切削用量手冊(cè)》表25,選擇ne = 2.5r/s, vfe =3.92mm/s 因此實(shí)際切削速度和每齒進(jìn)給量為: Ve= (5-2) afe= vfe /(z.ne)=3.92/8/5=0.1mm/z (5-3) (5)校驗(yàn)機(jī)床功率 根據(jù)表《切削用量手冊(cè)》表17,當(dāng)銑削寬度≤170mm,銑削深度ap≤4.2mm,d=200mm,齒數(shù)z=8, vfe =3
54、.92m/s,近似為Pe=5.2kw. 根據(jù)X52K型立銑說(shuō)明書,機(jī)床主軸允許的功率為P=10kwX0.75=7.5kw,故Pe<P,因此所選擇的切削用量可以采用。 (6).計(jì)算基本工時(shí)tm 根據(jù)公式: tm=L/vfe (5-3) 其中L=l+y+△, vfe =3.92mm/s,根據(jù)《切削用量手冊(cè)》表20,不對(duì)稱安裝銑刀,入切量及超切量y+△=60mm,則L=240mm.則基本工時(shí)為 tm=240/3.92=61.22s (7).準(zhǔn)備與終結(jié)時(shí)間te為:
55、 由《機(jī)械加工工藝手冊(cè)》表5.2經(jīng)驗(yàn)公式得 te=0.15tm=9.2s (5-4) (8).布置工作地時(shí)間與休息生理時(shí)間: 由《機(jī)械加工工藝手冊(cè)》表5.2-46得共占作業(yè)時(shí)間百分比(α+β)=15.9% 故工序5的單件時(shí)間定額由《機(jī)械加工工藝手冊(cè)》P5-19公式 ti=(tm+te)﹛1+(α+β)/100﹜ (5-5) ti =(61.22+9.2)(1+0.159)=81.62s 5.
56、1.2精銑上平面 計(jì)算銑削用量: (1)選擇刀具: 根據(jù)《切削用量手冊(cè)》表2,選擇YT15硬質(zhì)合金刀片。 根據(jù)《切削用量手冊(cè)》P110表1,銑削深度ap≤4mm時(shí),端銑刀直徑為80mm,銑削寬度為60mm,但實(shí)際要求銑削寬度為170mm,故因根據(jù)實(shí)際銑削寬度170mm,則端銑刀直徑為200mm,由于采用標(biāo)準(zhǔn)硬質(zhì)合金端銑刀,故齒數(shù)為z=8. (2)銑刀幾何形狀:由《切削用量手冊(cè)》P114 表2,端銑刀主偏角Kr=20°,端銑刀后角α0=6°,端銑刀副偏角Kr’=5°,端銑刀副后角α0’=8°,端銑刀前角 選擇切削用量: (1)決定銑削
57、深度ap 由于加工余量不大,故可在一次走刀內(nèi)銑完,故ap=h=0.7mm (2)決定每齒進(jìn)給量 采用不對(duì)稱端銑,以提高進(jìn)給量。根據(jù)《切削用量手冊(cè)》P118表5,當(dāng)使用YT15時(shí),銑床功率為10kw(X53K立銑說(shuō)明書,《切削用量手冊(cè)》表25)時(shí),每齒進(jìn)給量af=0.09~0.18mm/z,但因采用不對(duì)稱端銑,取0.18mm/z。 (3)選擇銑刀磨鈍標(biāo)準(zhǔn)及耐用度 根據(jù)《切削用量手冊(cè)》P119表7,銑刀刀齒后刀面最大磨損為1.0mm.由于銑刀直徑d=200mm,故耐用度T為240min.. (4)決定切削速度v和每秒鐘進(jìn)給量 根據(jù)《切削用量手冊(cè)》表13,當(dāng)銑刀直徑d=200mm,齒數(shù)
58、z=8mm, 銑削深度ap≤4mm, 每齒進(jìn)給量af≤0.24mm/z時(shí),vi =1.72m/s, ni=2.74rps, vfi=4.60mm/s. 再乘以各修正系數(shù)為《切削用量手冊(cè)》P132表13 故 v=vixkv=1.72x1.0x0.8=1.376m/s n=nixkn=2.74x1.0x0.8=2.192r/s vf=vfixkvf=4.6x1.0x0.8=3.68m/s 根據(jù)X53K立銑說(shuō)明書《切削用量手冊(cè)》表25,選擇ne = 2.5r/s, vfe =3.92mm/s 因此實(shí)際切削速度和每齒進(jìn)給量為: Ve= afe= vfe /(z.ne)=3.92/8/5
59、=0.1mm/z (5)校驗(yàn)機(jī)床功率 根據(jù)表《切削用量手冊(cè)》表17,當(dāng)銑削寬度≤170mm,銑削深度ap≤4.2mm,d=200mm,齒數(shù)z=8, vfe =3.92m/s,近似為Pe=5.2kw. 根據(jù)X52K型立銑說(shuō)明書,機(jī)床主軸允許的功率為P=10kwX0.75=7.5kw,故Pe<P,因此所選擇的切削用量可以采用。 (6).計(jì)算基本工時(shí)tm 根據(jù)公式: tm=L/vfe 其中L=l+y+△, vfe =3.92mm/s,根據(jù)《切削用量手冊(cè)》表20,不對(duì)稱安裝銑刀,入切量及超切量y+△=60mm,則L=240mm
60、.則基本工時(shí)為 tm=240/3.92=61.22s (7).準(zhǔn)備與終結(jié)時(shí)間te為: 由《機(jī)械加工工藝手冊(cè)》表5.2經(jīng)驗(yàn)公式得 te=0.15tm=9.2s (8).布置工作地時(shí)間與休息生理時(shí)間: 由《機(jī)械加工工藝手冊(cè)》表5.2-46得共占作業(yè)時(shí)間百分比(α+β)=15.9% 故工序5的單件時(shí)間定額由《機(jī)械加工工藝手冊(cè)》P5-19公式 ti=(tm+te)﹛1+(α+β)/100﹜ ti =(61.22+9.2)(1+0.159)=81.62s 5.2銑分割面690mmx300
61、mm 工件材料:HT200灰鑄鐵 工件尺寸:長(zhǎng)度l=690mm寬度ae=300mm平面 加工要求:銑箱蓋分割面,留磨余量0.5mm 機(jī)床:立式銑床X53K 刀具:采用標(biāo)準(zhǔn)硬質(zhì)合金端銑刀 加工余量:粗銑4mm,精銑1.7mm 5.2.1粗銑分割面 計(jì)算銑削用量: (1)選擇刀具 根據(jù)《切削用量手冊(cè)》表2,選擇YT15硬質(zhì)合金刀片。 根據(jù)《切削用量手冊(cè)》P110表1,銑削深度ap≤4mm時(shí),端銑刀直徑為80mm,銑削寬度為60mm,但實(shí)際要求銑削寬度ae為300mm,故因根據(jù)實(shí)際銑削寬ae為300mm,鉆則端銑刀直徑為400mm,由于采用標(biāo)準(zhǔn)硬質(zhì)合金端銑刀,由《切削用量手冊(cè)》
62、表13,故齒數(shù)為z=10. (2)銑刀幾何形狀:由《切削用量手冊(cè)》P114 表2,端銑刀主偏角Kr=20°,端銑刀后角α0=6°,端銑刀副偏角Kr’=5°,端銑刀副后角α0’=8°,端銑刀前角 選擇切削用量: (1)決定銑削深度ap 由于加工余量不大,故可在一次走刀內(nèi)銑完,故ap=h=4mm (2)決定每齒進(jìn)給量 采用不對(duì)稱端銑,以提高進(jìn)給量。根據(jù)《切削用量手冊(cè)》P118表5,當(dāng)使用YT15時(shí),銑床功率為10kw(X53K立銑說(shuō)明書,《切削用量手冊(cè)》表25)時(shí),每齒進(jìn)給量af=0.09~0.18mm/z,但因采用不對(duì)稱端銑,取0.18
63、mm/z. (3)選擇銑刀磨鈍標(biāo)準(zhǔn)及耐用度 根據(jù)《切削用量手冊(cè)》P119表7,銑刀刀齒后刀面最大磨損為1.5mm.由于銑刀直徑d=400mm,故耐用度T為18.0X1000S (4)決定切削速度v和每秒鐘進(jìn)給量 根據(jù)《切削用量手冊(cè)》表13,當(dāng)銑刀直徑d=400mm,齒數(shù)z=10, 銑削深度ap≤4mm, 每齒進(jìn)給量af≤0.24mm/z時(shí),vi =1.64m/s, ni=1.66rps, vfi=3.49mm/s. 再乘以各修正系數(shù)為《切削用量手冊(cè)》P132表13 故v=vi x kv=1.64x1.0x0.8=1.312m/s n=ni x kn=1.66x1.0x0.8=
64、1.328r/s vf=vfi x kvf=3.49x1.0x0.8=2.79mm/s 根據(jù)X53K立銑說(shuō)明書《切削用量手冊(cè)》表25,選擇ne = 1.58r/s, vfe =3.17mm/s因此實(shí)際切削速度和每齒進(jìn)給量為: Ve= afe= vfe /(z.ne)=3.17/10/1.58=0.2mm/z (5)校驗(yàn)機(jī)床功率 根據(jù)表《切削用量手冊(cè)》表17,當(dāng)銑削寬度≤170mm,銑削深度ap≤4.2mm,d=200mm,齒數(shù)z=10, vfe =3.17mm/s,近似為Pe=5.6kw 根據(jù)X52K型立銑說(shuō)明書,機(jī)床主軸允許的功率為P=10kwX0.75=7.5kw 故
65、Pe<P,因此所選擇的切削用量可以采用。 (6)計(jì)算基本工時(shí)tm tm=L/vfe 其中L=l+y+△, vfe =3.17mm/s,根據(jù)《切削用量手冊(cè)》表20,不對(duì)稱安裝,入切量及超切量y+△=117mm,則L=807mm,則基本工時(shí)為tm=807/3.17=254.57s (7).準(zhǔn)備與終結(jié)時(shí)間te為: 由《機(jī)械加工工藝手冊(cè)》表5.2經(jīng)驗(yàn)公式得 te=0.15tm=38.19s (8).布置工作地時(shí)間與休息生理時(shí)間: 由《機(jī)械加工工藝手冊(cè)》表5.2-46得α+β=15.9%,故工序5的單件時(shí)間 ti=(tm+te)﹛1+(α+β)/100﹜ ti =(
66、254.57+38.19)(1+0.159)=339.31s 5.2.2精銑分割面 計(jì)算銑削用量: (1)選擇刀具 根據(jù)《切削用量手冊(cè)》表2,選擇YT15硬質(zhì)合金刀片。 根據(jù)《切削用量手冊(cè)》P110表1,銑削深度ap≤4mm時(shí),端銑刀直徑為80mm,銑削寬度為60mm,但實(shí)際要求銑削寬度ae為300mm,故因根據(jù)實(shí)際銑削寬ae為300mm,鉆則端銑刀直徑為400mm,由于采用標(biāo)準(zhǔn)硬質(zhì)合金端銑刀,由《切削用量手冊(cè)》表13,故齒數(shù)為z=10. (2)銑刀幾何形狀:由《切削用量手冊(cè)》P114 表2,端銑刀主偏角Kr=20°,端銑刀后角α0=6°,端銑刀副偏角K
67、r’=5°,端銑刀副后角α0’=8°,端銑刀前角 選擇切削用量: (1)決定銑削深度ap 由于加工余量不大,故可在一次走刀內(nèi)銑完,故ap=h=1.7mm (2)決定每齒進(jìn)給量 采用不對(duì)稱端銑,以提高進(jìn)給量。根據(jù)《切削用量手冊(cè)》P118表5,當(dāng)使用YT15時(shí),銑床功率為10kw(X53K立銑說(shuō)明書,《切削用量手冊(cè)》表25)時(shí),每齒進(jìn)給量af=0.09~0.18mm/z,但因采用不對(duì)稱端銑,取0.18mm/z. (3)選擇銑刀磨鈍標(biāo)準(zhǔn)及耐用度 根據(jù)《切削用量手冊(cè)》P119表7,銑刀刀齒后刀面最大磨損為1.5mm.由于銑刀直徑d=400mm,故耐用度T為18.0X1000S (4)決定切削速度v和每秒鐘進(jìn)給量 根據(jù)
- 溫馨提示:
1: 本站所有資源如無(wú)特殊說(shuō)明,都需要本地電腦安裝OFFICE2007和PDF閱讀器。圖紙軟件為CAD,CAXA,PROE,UG,SolidWorks等.壓縮文件請(qǐng)下載最新的WinRAR軟件解壓。
2: 本站的文檔不包含任何第三方提供的附件圖紙等,如果需要附件,請(qǐng)聯(lián)系上傳者。文件的所有權(quán)益歸上傳用戶所有。
3.本站RAR壓縮包中若帶圖紙,網(wǎng)頁(yè)內(nèi)容里面會(huì)有圖紙預(yù)覽,若沒(méi)有圖紙預(yù)覽就沒(méi)有圖紙。
4. 未經(jīng)權(quán)益所有人同意不得將文件中的內(nèi)容挪作商業(yè)或盈利用途。
5. 裝配圖網(wǎng)僅提供信息存儲(chǔ)空間,僅對(duì)用戶上傳內(nèi)容的表現(xiàn)方式做保護(hù)處理,對(duì)用戶上傳分享的文檔內(nèi)容本身不做任何修改或編輯,并不能對(duì)任何下載內(nèi)容負(fù)責(zé)。
6. 下載文件中如有侵權(quán)或不適當(dāng)內(nèi)容,請(qǐng)與我們聯(lián)系,我們立即糾正。
7. 本站不保證下載資源的準(zhǔn)確性、安全性和完整性, 同時(shí)也不承擔(dān)用戶因使用這些下載資源對(duì)自己和他人造成任何形式的傷害或損失。
最新文檔
- 6.煤礦安全生產(chǎn)科普知識(shí)競(jìng)賽題含答案
- 2.煤礦爆破工技能鑒定試題含答案
- 3.爆破工培訓(xùn)考試試題含答案
- 2.煤礦安全監(jiān)察人員模擬考試題庫(kù)試卷含答案
- 3.金屬非金屬礦山安全管理人員(地下礦山)安全生產(chǎn)模擬考試題庫(kù)試卷含答案
- 4.煤礦特種作業(yè)人員井下電鉗工模擬考試題庫(kù)試卷含答案
- 1 煤礦安全生產(chǎn)及管理知識(shí)測(cè)試題庫(kù)及答案
- 2 各種煤礦安全考試試題含答案
- 1 煤礦安全檢查考試題
- 1 井下放炮員練習(xí)題含答案
- 2煤礦安全監(jiān)測(cè)工種技術(shù)比武題庫(kù)含解析
- 1 礦山應(yīng)急救援安全知識(shí)競(jìng)賽試題
- 1 礦井泵工考試練習(xí)題含答案
- 2煤礦爆破工考試復(fù)習(xí)題含答案
- 1 各種煤礦安全考試試題含答案
相關(guān)資源
更多