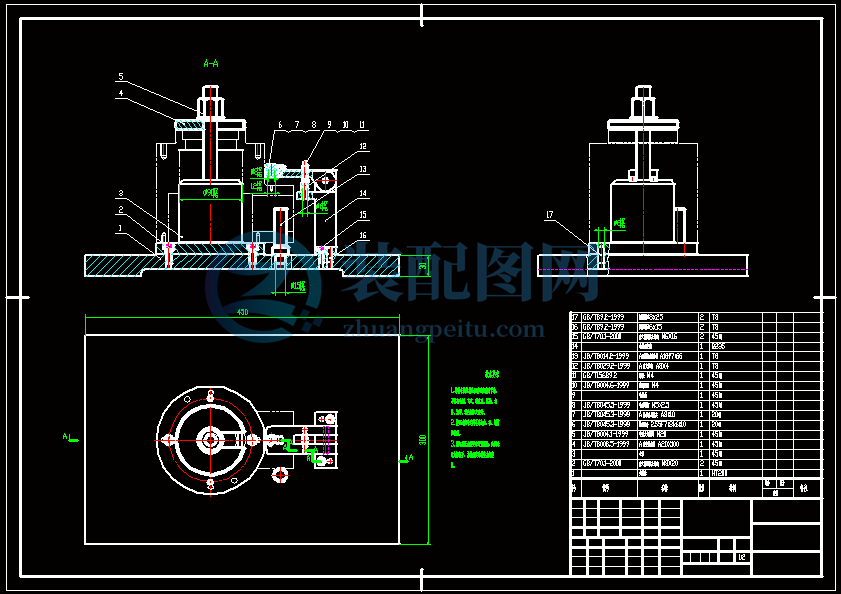
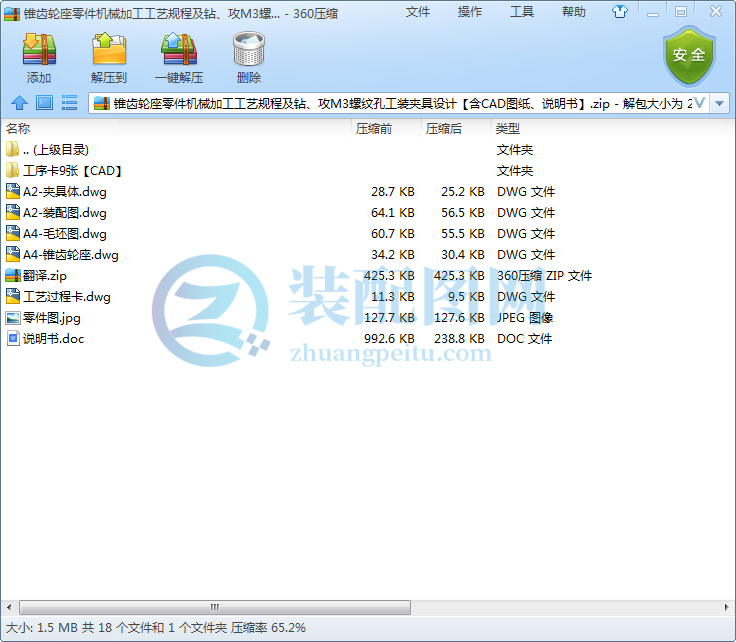

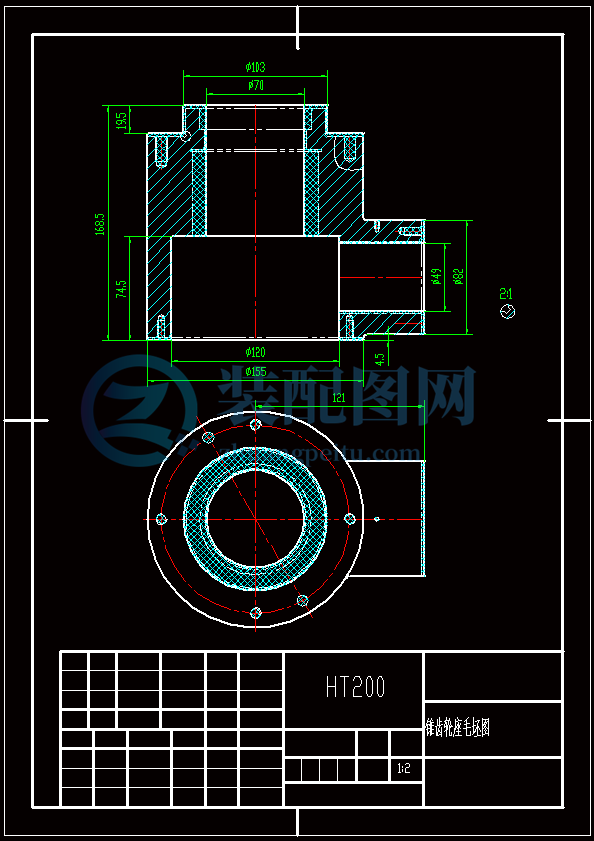

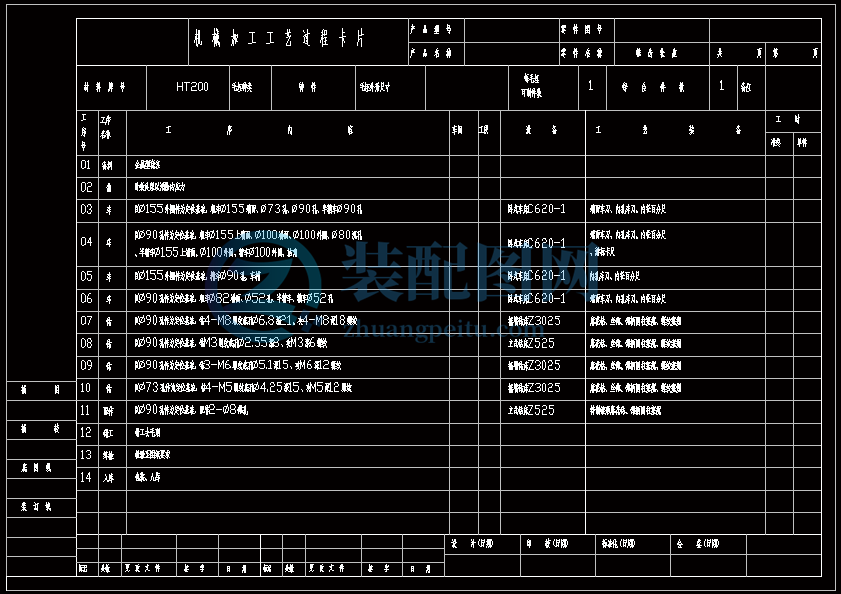

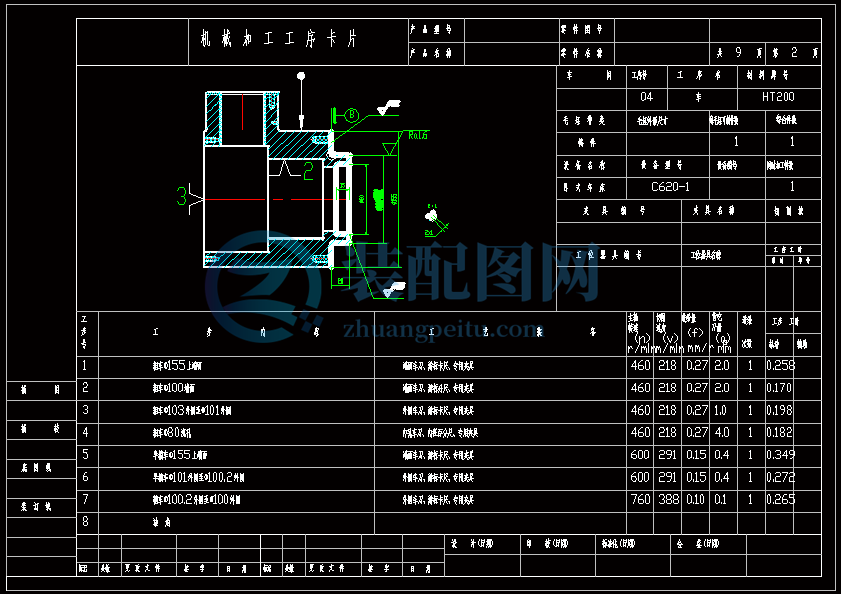



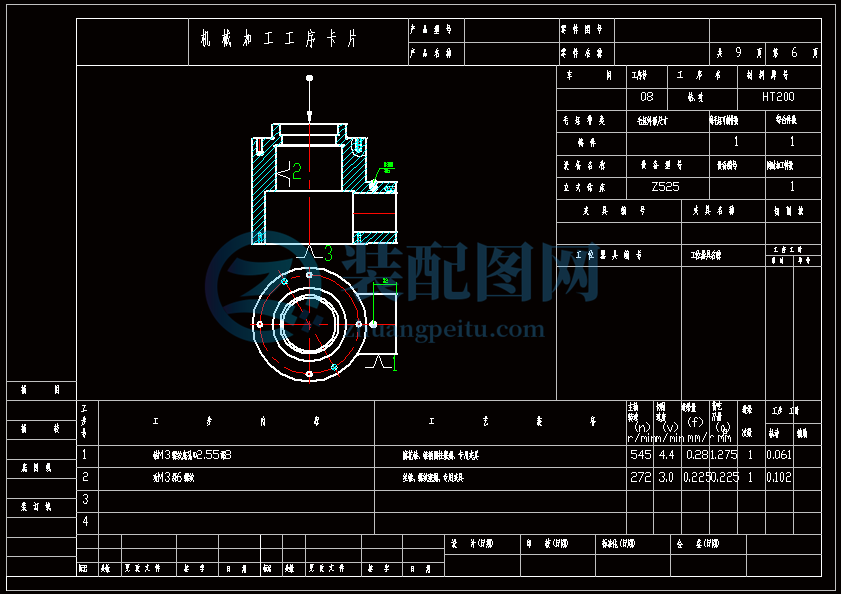
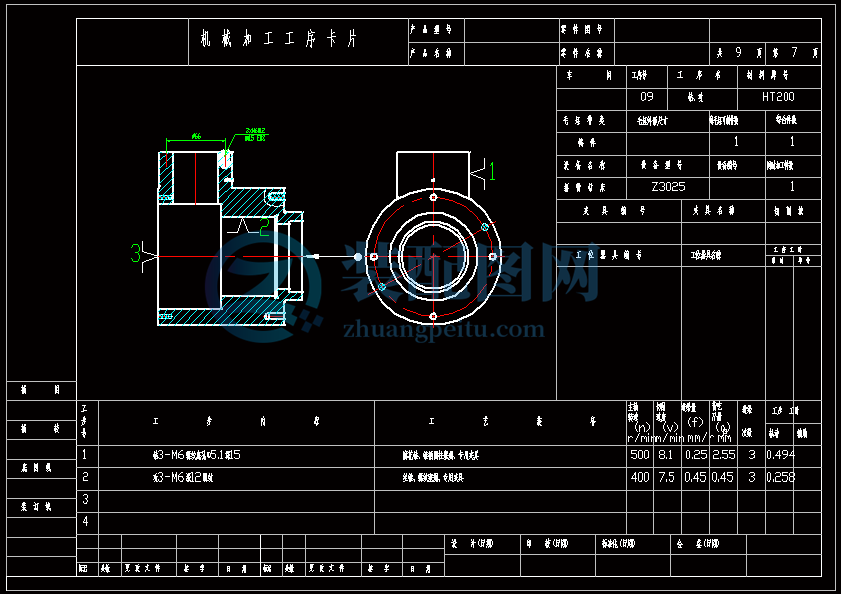


目 錄 前 言 .......................................................1 1 概述發(fā)展 ..................................................2 1.1 機床夾具簡介 ..........................................2 1.1.1 機床夾具的主要功能 ................................2 1.1.2 機床夾具的組成 ....................................2 1.1.3 夾具設計的步驟和基本要求 ..........................2 2 錐齒輪座的加工工藝規(guī)程設計 ................................8 2.1 錐齒輪座的作用 ........................................8 2.2 零件的工藝分析 ........................................8 2.3 基面的選擇 ............................................8 2.3.1 粗基準的選擇原則 ..................................8 2.3.2 精基準選擇的原則 ..................................9 2.4 制定工藝路線 ..........................................9 2.5 確定各工序的加工余量、計算工序尺寸及公差 .............10 2.6 確定切削用量及基本工時 ...............................13 3 專用夾具設計 .............................................23 3.1 問題提出 .............................................23 3.2 定位基準的選擇 .......................................23 3.3 定位元件的設計 .......................................23 3.4 定位誤差分析 .........................................23 3.5 切削力的計算與夾緊力分析 .............................24 3.6 鉆套設計 .............................................25 3.7 夾具設計及操作簡要說明 ...............................26 結束語 .....................................................27 謝 辭 ......................................................28 參 考 文 獻 ................................................29 0 前 言 機械制造業(yè)是制造具有一定形狀位置和尺寸的零件和產(chǎn)品,并把它們裝備成 機械裝備的行業(yè)。機械制造業(yè)的產(chǎn)品既可以直接供人們使用,也可以為其它行業(yè) 的生產(chǎn)提供裝備,社會上有著各種各樣的機械或機械制造業(yè)的產(chǎn)品。我們的生活 離不開制造業(yè),因此制造業(yè)是國民經(jīng)濟發(fā)展的重要行業(yè),是一個國家或地區(qū)發(fā)展 的重要基礎及有力支柱。從某中意義上講,機械制造水平的高低是衡量一個國家 國民經(jīng)濟綜合實力和科學技術水平的重要指標。 錐齒輪座及其鉆、攻 M3 螺紋孔的夾具設計是在學完了機械制圖、機械制造技 術基礎、機械設計、機械工程材料等進行畢業(yè)設計之后的下一個教學環(huán)節(jié)。正確 地解決一個零件在加工中的定位,夾緊以及工藝路線安排,工藝尺寸確定等問題, 并設計出專用夾具,保證零件的加工質(zhì)量。本次設計也要培養(yǎng)自己的自學與創(chuàng)新 能力。因此本次設計綜合性和實踐性強、涉及知識面廣。所以在設計中既要注意 基本概念、基本理論,又要注意生產(chǎn)實踐的需要,只有將各種理論與生產(chǎn)實踐相 結合,才能很好的完成本次設計。 本設計選用錐齒輪座來進行工藝編制與夾具設計,以說明書、繪圖為主,設計 手冊與國家標準為附來進行詳細說明。 1 1 概述發(fā)展 1.1 機床夾具簡介 1.1.1 機床夾具的主要功能 機床夾具已成為機械加工時的重要裝備,同時是機械加工不可缺少的部件, 在機床技術向高速、高效、精密、復合、智能、環(huán)保方向發(fā)展的帶動下,夾具技 術也正朝著高精、高效、模塊、組合、通用 、經(jīng)濟方向發(fā)展。機床夾具的主要功 能是使工件定位夾緊,使工件相對于刀具及機床占有正確的加工位置,保證其被 加工表面達到工序所規(guī)定的技術要求,工件定位后,經(jīng)夾緊裝置施力于工件,將 其固定夾牢,使其在加工過程中不致因切削力、重力、離心力等外力作用而發(fā)生 位置改變。為了適應不同行業(yè)的需求和經(jīng)濟性,夾具有不同的型號,以及不同檔 次的精度標準供選擇。 安裝方法有找正法和用專用夾具,找正法用于單件、小批生產(chǎn)中,而專用夾 具用于生產(chǎn)批量較大或特殊需要時。 1.1.2 機床夾具的組成 1)定位支承元件 確定工件在夾具中的正確位置并支承工件。 2)夾緊裝置 將工件夾緊不發(fā)生移動。 3)對刀或導向元件 保證刀具與工件加工表面的正確位置。 4)夾具體 將夾具的所有組成部分組成一體,并保證它們之間的相對位置關系。 1.1.3 夾具設計的步驟和基本要求 一:夾具設計的基本要求 夾具在機械加工中起著重要的作用,它直接影響機械加工的質(zhì)量、工人的勞 動強度、生產(chǎn)率和加工成本。因此對設計的夾具,提出以下幾點基本要求。 1)能穩(wěn)定可靠地保證工件的加工技術要求。若工件達不到加工技術要求,成 為廢品,則夾具設計是失敗的,該夾具不能用與生產(chǎn)。 2)操作簡單,便于工件安裝,減輕工人的勞動強度,節(jié)省工件安裝時間,降 低輔助工時,保證高的生產(chǎn)效率。 3)具有良好的工藝性,便于制造,降低夾具制造成本,從而降低分攤在工件 上的加工成本。 2 為保證上述基本要求,夾具的生產(chǎn)過程應按下面程序進行:夾具生產(chǎn)任務書 夾具的結構設計使用、制造部門會簽夾具制造夾具驗收生產(chǎn)使 用。 夾具生產(chǎn)任務書是由工藝人員在編制工藝規(guī)程時,根據(jù)生產(chǎn)需要而提出的。 任務書中包含內(nèi)容有設計理由、使用車間、使用設備,該夾具所使用工件工序的 工序圖并在工序圖上要標明工序要求、加工表面、尺寸精度要求及定位定位基準、 夾緊點。這是設計夾具的依據(jù),也是驗收制造夾具的依據(jù)。夾具結構設計是設計 人根據(jù)夾具設計任務書的加工要求,提出幾種可行方案、分析比較、進行誤差計 算,以確定出合理方案,進行設計。夾具結構設計完成后,要會同使用部門、制 造部門就夾具的結構合理性、結構工藝性和經(jīng)濟性進行審核、會簽、交付制造。 制成的夾具要同設計人員。工藝人員、使用部門、制造部門共同進行驗證。當確 認夾具可保證工件該工序加工要求,能保證生產(chǎn)率、操作方便、安全,就可交付 生產(chǎn)車間使用。 二:夾具的設計步驟 當接到夾具設計任務書后,按下面 6 個步驟,逐步設計。 1)明確設計任務,收集研究設計的原始資料。原始資料包括如下內(nèi)容。 A:加工零件的零件圖、毛坯圖及加工工藝過程,所設計夾具應有的工序圖,并 了解該工序所使用的設備、刀具、量具、其他輔具以及該工序的加工余量、切削 用量、加工要求、生產(chǎn)節(jié)拍等參數(shù)。 B:了解零件的生產(chǎn)類型,就是決定夾具采用簡單結構或復雜結構的依據(jù)。若屬 大批量生產(chǎn),則力求夾具結構完善、生產(chǎn)率高 或是單件小批量生產(chǎn)或急于應付生 產(chǎn),則夾具結構應簡單,以便迅速制造交付使用。 C:收集該夾具所用機床的資料,主要指與夾具連接部分的安裝尺寸。如銑床夾 具要安裝在工作臺上,要收集工作如大小,工作如 T 形槽及槽距,以及機床的技 術參數(shù)。 D:收集所使用刀具的資料如刀具的精度、安裝方式、使用要求及技術條件等。 E:收集國內(nèi)外同類型夾具資料,吸收其中先進而又能結合本廠情況的合理部分。 F:了解本廠制造夾具的能力和使用的條件,如夾具制造的條件及精度水平,有 無壓縮空氣壓值等。 3 G:收集有關夾具部件的標準(包括國標、部標、企標、廠標),典型夾具結構 圖冊等。 2)確定夾具結構方案,繪制結構草圖,其主要內(nèi)容如下。 A:根據(jù)工件加工尺寸、要求和開關,確定工件的定位方式,選擇或設計定位元 件,計算定位誤差。 B:確定刀具的引導方式及引導元件(指鉆夾具、銑夾具)。 C:確定工件夾緊方式 ,選擇或設計夾緊機構,計算夾緊力。 D:確定其他裝置(如分度裝置、頂出裝置)的結構型式。 E:確定和設計其他結構,如銑床夾具與機床的連接裝置、對刀裝置。 在確定夾具結構的各組成部分時,可提出幾種不同方案,分別畫出草圖,進行分 析比較,從中選擇出合理方案。 3)繪制夾具總圖。應注意以下幾點。 A:繪制夾具總圖,盡量按 1:1 繪制,以保證直觀性。 B:主視圖盡量符合操作者的正面位置。 C:工件輪廓用雙點畫線繪制,并視為假想透明體,不影響其他元件的繪制。 D:繪圖順序為:工件定位元件引導元件夾緊裝置其他裝置 夾具體。 4)標注總圖上的尺寸、公差與配合和技術條件。夾具總圖結構繪制完成后,需標 注五類尺寸和四類技術條件。 5)編寫零件明細表。明細表應包括零件序號、名稱、代號(指標準件代號或通用 件代號 )、數(shù)量、材料、熱處理、質(zhì)量等。 6)繪制總圖中非標準件的零件圖。 三:夾具總圖上尺寸、公差與配合和技術條件的標注 在夾具設計中,對于初設計者,在夾具總圖上如何標注尺寸及技術條件,往往是 難點之一,以下對此作簡要闡述。 1)夾具總圖上應標注的五類尺寸 A:夾具外形輪廓尺寸指夾具在長、寬、高三個方向上的最大極限尺寸。若有 可動部分,則指運動部件在空間達到的極限位置的尺寸。標注夾具外形尺寸的目 的是避免夾具與機床或刀具在空間發(fā)生干涉。 B:工件與定位元件間的聯(lián)系尺寸主要指工件定位面與定位元件工作面的配合 4 尺寸或各定位元件的位置尺寸,它們直接影響工件加工精度,是計算工件定位誤 差的依據(jù)。 C:夾具與刀具的聯(lián)系尺寸主要指對刀元件或引導元件與夾具定位元件之間的 位置尺寸、引導元件之間的位置尺寸或引導與導向部分的配合尺寸。 D:夾具與機床的連接部分尺寸這類尺寸主要指夾具與機床主軸或工作如必須 固定連接的平俱。如車床夾具要安裝在車床主軸上,要標注與車床主軸的連接尺 寸,銑床夾具要安裝在工作臺上,要標注與工作如 T 形槽相配的定位鍵尺寸。 E:夾具內(nèi)容的配合尺寸中心軸與夾具體孔的配合尺寸,鉆套與襯套、襯套與 夾具體的配合尺寸,此類尺寸必須標注尺寸、配合性質(zhì)及配合精度,否則夾具精 度無法保證。 2) 夾具總圖上應標注的四類技術條件 夾具中的技術條件主要指夾具裝配好后,各表面之間的位置精度要求。 A:定位元件之間的相互位置要求這是指組合定位時多個定位元件之間的相互 位置要求或多件裝夾時相同定位元件之間的相互位置要求。如兩端頂尖頂軸兩端 中心孔,要求兩頂尖軸線同軸度,兩 V 形塊對稱線的同軸度。 B:定位元件與連接元件或夾具體底面的相位置要求夾具的連接元件或夾具體 底面是夾具與機床的連接部分,它決定了夾具與機床的相對位置,也就是決定了 定位元件相對機床,或刀具的位置,即決定了工件相對機床或刀具的位置。 C:引導元件與連接元件或夾具體底面的位置要求 D:引導元件與定位元件之間的相互位置要求 3)五類尺寸、四類技術條件的分類 五類尺寸、四類技術條件根據(jù)是否與工序加工要求相關而分為兩類,其精度值大 小和取法不同。 A:與工件加工要求無直接關系的 尺寸公差與配合 這類尺寸公差與配合應按照元件在夾具中的功用和裝配要求, 根據(jù)公差與配合國家標準或參閱有關資料來制定。 技術條件 與工件加工要求無直接關系的夾具上技術條件。 B: 與加工要求直接相關的 這類尺寸和技術條件與工件上相應尺寸和技術條件 直接對應,直接根據(jù)工件相應尺寸公差和相互位置允差的(1/51/2)的值選取。 一般工件允差小,取大系數(shù),工件允差大,則取小系數(shù)。 5 制定這類夾具尺寸公差時,要注意下列問題。 應經(jīng)工件的平均尺寸作為夾具相應尺寸的基本尺寸,極限偏差按對稱雙向標注。 應以工序尺寸(不一定是工件最終尺寸)作為夾具基本尺寸的設計依據(jù)。 4)夾具調(diào)刀尺寸的標注 當夾具設計完成,按要求標注尺寸后,對有些夾具如銑夾具,往往還要標注調(diào)刀 尺寸(調(diào)刀尺寸一般是指夾具的調(diào)刀基準到對刀元件工作表面的位置尺寸),即 刀具相對基準的尺寸,它與工件加工尺寸直接相關,也是夾具總圖上關鍵尺寸要 求。 四:夾具體設計 夾具總體設計中最后完成的主要元件是夾具體。夾具體是夾具基礎件、組成夾具 的各種元件、機構、裝置都要安裝在夾具體上。在加工過程中,它還要承受切削 力、夾緊、慣性力及由此而產(chǎn)生的振動和沖擊。所以,夾具體是夾具中一個設計、 制造勞動量大,耗費材料多,加工要求高的零部件。在夾具成本中所占比重較大, 制造周期也長,設計時,應給以足夠的重視。 (1) 夾具體和毛坯結構 實際生產(chǎn)中所用夾具體常用的有三種結構。 A:鑄造結構 鑄造結構夾具體的優(yōu)點如下: 可鑄出復雜的結構形狀。 鑄件抗壓強度大、抗振性好,特別適用于加工時振動大、切削負荷大的場合。 鑄件易于加工,價格低廉,成本低。但鑄件生產(chǎn)周期長,因存在鑄內(nèi)應力,易 引起變形,影響夾具精度的保持性,因此,夾具體必須進行時效處理。 B:焊接結構其優(yōu)點如下: 容易制造,周期短。 采用鋼板、型材,如結構合理,布置得當,可減小質(zhì)量。由于上述兩優(yōu)點,特 別適用于新產(chǎn)品試制或臨時急用的場合,以縮短生產(chǎn)周期。此外,一些結構簡單 的小型夾具,如翻轉式鉆模、蓋板式鉆模、可缷式鉆模,采用焊接式結構十分有 利,因為這些夾具要頻繁拆缷翻轉,力求結構輕巧耐磨。 但焊接結構夾具體在焊接過程中的熱變形和殘余應力對夾具精度會有不得影響, 6 因此,焊完后要進行退火處理;另外,為提高剛性需加加強筋。 C:裝配結構 裝配夾具體是選用夾具專用標準毛坯或標準零件,根據(jù)使用要求組裝而成,可得 到精確的外形和空間位置尺寸。標準毛坯和標準零件可組織專業(yè)化生產(chǎn),這樣不 但可以大大縮短夾具體的生產(chǎn)周期,還可降低生產(chǎn)成本。要使裝配夾具體在生產(chǎn) 中得到廣泛使用,必須實行夾具零部件的標準化、系列化。 (2)對夾具體的基本要求 A:一定的形狀和尺寸 夾具的外形,取決于安裝在夾具上的各種元件、機構、裝置的形狀及它們之間的 布置位置。設計時,只要將組成該夾具的所有元件、機構和裝置的結構尺寸都設 計好并布置好它們在圖紙上的位置,就可以由此勾畫出夾具體的大致外形輪廓尺 寸。因為是單件生產(chǎn),一般不作復雜計算設計。通常參照類似的夾具結構,按經(jīng) 驗類比法估計確定。 確定夾具體尺寸時,可參考下面數(shù)據(jù)。 鑄造結構的夾具體,壁厚取 1540mm,過厚處挖空。 焊接結構用鋼板取 1015mm,剛度不夠時加筋板。 夾具體上不加工表面與工件表面之間應有一定間隙,以保證工件與夾具體之間 不發(fā)生干涉。間隙大小按以下規(guī)定選?。?a:夾具體、工件都是毛面,間隙取 815mm. b:夾具體是毛面,工件是光面,間隙取 410mm. B:足夠的強度和剛度 目的是減小在加工過程中因受切削力、夾緊力等而發(fā)生變形或振動。當剛度不夠 時,可增設加強筋或用框形結構。若用加強筋,其壁厚取 0.70.9 倍壁厚,高度 不大于壁厚 5 倍。 C:良好的結構工藝性 以便于制造、裝配、并減少加工工時。如夾具體上大平面上要局部加工,可鑄出 35mm 凸臺;各加工表面,最好在同一平面內(nèi)或在同一回轉表面上,以便于加工; 盡量減少加工表面面積。另外,對于切削量大的工件所使用夾具,要注意應能方 便排屑,以免影響安裝精度;對于大而重的夾具體,要考慮起吊裝置,如吊環(huán)螺 釘或起重螺栓。 7 2 錐齒輪座的加工工藝規(guī)程設計 2.1 錐齒輪座的作用 錐齒輪座是一個典型的交叉孔零件,主要應用在混凝土拖泵中導向輪部件上, 其上要安裝兩個配對錐齒輪座,因此主要的工作表面為 90mm 和 52mm 的兩個 孔。 2.2 零件的工藝分析 對該零件的平面、孔和螺紋進行加工,具體要求如下: 155 下端面 粗糙度 Ra6.3 73 孔 粗糙度 Ra6.3 90 孔 粗糙度 Ra1.6 155 上端面 粗糙度 Ra3.2 100 端面 粗糙度 Ra6.3 100 外圓 粗糙度 Ra1.6 80 沉孔 粗糙度 Ra6.3 82 端面 粗糙度 Ra6.3 52 孔 粗糙度 Ra1.6 4-M8 螺紋 粗糙度 Ra12.5 M3 螺紋 粗糙度 Ra12.5 3-M6 螺紋 粗糙度 Ra12.5 4-M5 螺紋 粗糙度 Ra12.5 2-8 錐孔 粗糙度 Ra6.3 8 2.3 基面的選擇 基面的選擇是工藝規(guī)程設計中的重要工作之一?;孢x擇的正確、合理,可 以保證質(zhì)量,提高生產(chǎn)效率。否則,就會使加工工藝過程問題百出,嚴重的還會 造成零件大批報廢,使生產(chǎn)無法進行。 2.3.1 粗基準的選擇原則 1)如果必須首先保證工件上加工表面與不加工表面 之間的位置要求,應以不加 工表面作為粗基準。如果在工件上有很多不需加工的表面,則應以其中與加工面 位置精度要求較高的表面作粗基準。 2)如果必須首先保證工件某重要表面的加工余量均勻,應選擇該表面作精基準。 3)如需保證各加工表面都有足夠的加工余量,應選加工余量較小的表面作粗基準。 4)選作粗基準的表面應平整,沒有澆口、冒口、飛邊等缺陷,以便定位可靠。 5)粗基準一般只能使用一次,特別是主要定位基準,以免產(chǎn)生較大的位置誤差。 2.3.2 精基準選擇的原則 選擇精基準時要考慮的主要問題是如何保證設計技術要求的實現(xiàn)以及裝夾準 確、可靠、方便。 精基準選擇應當滿足以下要求: 1)用設計基準作為定位基準,實現(xiàn)“基準重合”,以免產(chǎn)生基準不重合誤差。 2)當工件以某一組精基準定位可以較方便地加工很多表面時,應盡可能采用 此組精基準定位,實現(xiàn)“基準統(tǒng)一”,以免生產(chǎn)基準轉換誤差。 3)當精加工或光整加工工序要求加工余量盡量小而均勻時,應選擇加工表面 本身作為精基準,即遵循“自為基準”原則。該加工表面與其他表面間的 位置精度要求由先行工序保證。 4)為獲得均勻的加工余量或較高 的位置精度,可遵循“互為基準”、反復 加工的原則。 5)有多種方案可供選擇時應選擇定位準確、穩(wěn)定、夾緊可靠,可使夾具結構 簡單的表面作為精基準。 9 2.4 制定工藝路線 制定工藝路線的出發(fā)點,應當是使零件的幾何形狀、尺寸精度及位置精 度等技術要求能得到合理的保證。在生產(chǎn)綱領以確定為大批生產(chǎn)的條件下, 可采用通用機床配以專用工夾具,并盡量使工序集中來提高生產(chǎn)效率。除此 以外,還應考慮經(jīng)濟效果,以便降低生產(chǎn)成本。 最終工藝方案如下: 工序 01:金屬型澆注 工序 02:時效處理以消除內(nèi)應力 工序 03:以 155 外圓作為定位基準,粗車 155 下端面、73 孔、90 孔、半精車 90 孔 工序 04:以 90 孔作為定位基準,粗車 155 上端面、100 端面、100 外圓、80 沉孔 、半精車 155 上端面、100 外圓、精車 100 外圓、潔角 工序 05:以 155 外圓作為定位基準,精車 90 孔、車槽 工序 06:以 90 孔作為定位基準,粗車 82 端面、52 孔、半精車、精車 52 孔 工序 07:以 90 孔作為定位基準,鉆 4-M8 螺紋底孔 6.8 深 21、攻 4-M8 深 18 螺紋 工序 08:以 90 孔作為定位基準,鉆 M3 螺紋底孔 2.55 深 8、攻 M3 深 6 螺紋 工序 09:以 90 孔作為定位基準,鉆 3-M6 螺紋底孔 5.1 深 15、攻 M6 深 12 螺紋 工序 10:以 73 孔作為定位基準,鉆 4-M5 螺紋底孔 4.25 深 15、攻 M5 深 12 螺紋 工序 11:以 90 孔作為定位基準,配作 2-8 錐孔 工序 12:鉗工去毛刺 工序 13:檢驗至圖紙要求 工序 14:包裝、入庫 2.5 確定各工序的加工余量、計算工序尺寸及公差 1. 155 下端面的加工余量 10 查機械制造工藝設計簡明手冊表 2.2-4,得鑄件的單邊加工余量 Z=2.5mm,鑄 件尺寸公差為 CT8 級,表面粗糙度 Ra 為 6.3。根據(jù)機械制造工藝設計簡明手冊 表 1.4-8,一步車削(即粗車、半精車)方可滿足其精度要求。 2. 73 孔的加工余量 查機械制造工藝設計簡明手冊表 2.2-4,得鑄件的單邊加工余量 Z=1.5mm,鑄 件尺寸公差為 CT8 級,表面粗糙度 Ra 為 6.3。根據(jù)機械制造工藝設計簡明手冊 表 1.4-8,一步車削(即粗車、半精車)方可滿足其精度要求。 3. 90 孔 的加工余量 查機械制造工藝設計簡明手冊表 2.2-4,得鑄件的單邊加工余量 Z=8.5mm,鑄 件尺寸公差為 CT8 級,表面粗糙度 Ra 為 1.6。根據(jù)機械制造工藝設計簡明手冊 表 1.4-8,三步車削(即粗車、半精車、精車)方可滿足其精度要求。 粗車 單邊余量 Z=8.0mm 半精車 單邊余量 Z=0.4mm 精車 單邊余量 Z=0.1mm 4. 155 上端面的加工余量 查機械制造工藝設計簡明手冊表 2.2-4,得鑄件的單邊加工余量 Z=2.5mm,鑄 件尺寸公差為 CT8 級,表面粗糙度 Ra 為 3.2。根據(jù)機械制造工藝設計簡明手冊 表 1.4-8,兩步車削(即粗車、半精車)方可滿足其精度要求。 粗車 單邊余量 Z=2.0mm 半精車 單邊余量 Z=0.5mm 5. 100 端面 的加工余量 查機械制造工藝設計簡明手冊表 2.2-4,得鑄件的單邊加工余量 Z=2.0mm,鑄 件尺寸公差為 CT8 級,表面粗糙度 Ra 為 6.3。根據(jù)機械制造工藝設計簡明手冊 表 1.4-8,一步車削(即粗車)方可滿足其精度要求。 6. 100 外圓的加工余量 查機械制造工藝設計簡明手冊表 2.2-4,得鑄件的單邊加工余量 Z=1.5mm,鑄 件尺寸公差為 CT8 級,表面粗糙度 Ra 為 1.6。根據(jù)機械制造工藝設計簡明手冊 表 1.4-8,三步車削(即粗車、半精車、精車)方可滿足其精度要求。 粗車 單邊余量 Z=1.0mm 半精車 單邊余量 Z=0.4mm 11 精車 單邊余量 Z=0.1mm 7.80 沉孔 的加工余量 查機械制造工藝設計簡明手冊表 2.2-4,得鑄件的單邊加工余量 Z=3.5mm,鑄 件尺寸公差為 CT8 級,表面粗糙度 Ra 為 6.3。根據(jù)機械制造工藝設計簡明手冊 表 1.4-8,一步車削(即粗車)方可滿足其精度要求。 8.82 端面加工余量 查機械制造工藝設計簡明手冊表 2.2-4,得鑄件的單邊加工余量 Z=2.0mm,鑄 件尺寸公差為 CT8 級,表面粗糙度 Ra 為 6.3。根據(jù)機械制造工藝設計簡明手冊 表 1.4-8,一步車削(即粗車)方可滿足其精度要求。 9.52 孔加工余量 查機械制造工藝設計簡明手冊表 2.2-4,得鑄件的單邊加工余量 Z=1.5mm,鑄 件尺寸公差為 CT8 級,表面粗糙度 Ra 為 1.6。根據(jù)機械制造工藝設計簡明手冊 表 1.4-8,三步車削(即粗車、半精車、精車)方可滿足其精度要求。 粗車 單邊余量 Z=1.0mm 半精車 單邊余量 Z=0.4mm 精車 單邊余量 Z=0.1mm 10. 4-M8 螺紋的加工余量 查機械制造工藝設計簡明手冊表 2.2-4,因其加工螺紋的尺寸不大故采 用實心鑄造,鑄件尺寸公差為 CT8 級,表面粗糙度 Ra 為 12.5。根據(jù)機械制造 工藝設計簡明手冊表 1.4-8,鉆.攻即可方可滿足其精度要求。 鉆 單邊余量 Z=3.4mm 攻 單邊余量 Z=0.6mm 11. M3 螺紋的加工余量 查機械制造工藝設計簡明手冊表 2.2-4,因其加工螺紋的尺寸不大故采 用實心鑄造,鑄件尺寸公差為 CT8 級,表面粗糙度 Ra 為 12.5。根據(jù)機械制造 工藝設計簡明手冊表 1.4-8,鉆.攻即可方可滿足其精度要求。 鉆 單邊余量 Z=1.275mm 攻 單邊余量 Z=0.225mm 12. 3-M6 螺紋的加工余量 查機械制造工藝設計簡明手冊表 2.2-4,因其加工螺紋的尺寸不大故采 12 用實心鑄造,鑄件尺寸公差為 CT8 級,表面粗糙度 Ra 為 12.5。根據(jù)機械制造 工藝設計簡明手冊表 1.4-8,鉆.攻即可方可滿足其精度要求。 鉆 單邊余量 Z=2.55mm 攻 單邊余量 Z=0.45mm 13. 4-M5 螺紋的加工余量 查機械制造工藝設計簡明手冊表 2.2-4,因其加工螺紋的尺寸不大故采 用實心鑄造,鑄件尺寸公差為 CT8 級,表面粗糙度 Ra 為 12.5。根據(jù)機械制造 工藝設計簡明手冊表 1.4-8,鉆.攻即可方可滿足其精度要求。 鉆 單邊余量 Z=2.125mm 攻 單邊余量 Z=0.375mm 14. 2-8 錐孔的加工余量 查機械制造工藝設計簡明手冊表 2.2-4,因其加工表面的尺寸不大故采 用實心鑄造,鑄件尺寸公差為 CT8 級,表面粗糙度 Ra 為 6.3。根據(jù)機械制造工 藝設計簡明手冊表 1.4-8,一步鉆削方可滿足其精度要求。 2.6 確定切削用量及基本工時 工序 01:金屬型澆注 工序 02:時效處理以消除內(nèi)應力 工序 03:以 155 外圓作為定位基準,粗車 155 下端面、73 孔、90 孔、半精車 90 孔 工步一:粗車 155 下端面 1、切削用量 機床為 C620-1 型臥式車床, 所選刀具為 YT5 硬質(zhì)合金端面車刀。根據(jù) 切削用量簡明手冊第一部分表 1.1,由于 C620-1 型臥式車床的中心高度為 200mm(表 1.30),故選刀桿尺寸 BH=16mm25mm,刀片厚度為 4.5mm。根據(jù)表 1.3,選擇車刀幾何形狀為卷屑槽帶倒棱型前刀面,前角 ,后角 ,01206a 主偏角 ,副偏角 ,刃傾角 ,刀尖圓弧半徑 。09rk01、rk0sm8. 1)確定切削深度 pa 由于單邊余量為 2.5mm,可在 1 次走刀內(nèi)切完。 13 2)確定進給量 f 根據(jù)表 1.4,在粗車 QT500-7、刀桿尺寸為 16mm25mm、 3mm、工件直徑pa 為 0100mm 時, =0.1 0.6mm/rf 按 C620-1 型臥式車床的進給量(表 4.2-9),選擇 =0.27mm/rf 確定的進給量尚需滿足機床進給機構強度的要求,故需進行校驗。 根據(jù)表 1.30,C620-1 機床進給機構允許的進給力 =3530N。maxF 根據(jù)表 1.21,當 2mm, 0.35mm/r, , =450m/min(預計)時,paf 045rk 進給力 =760N。fF 的修正系數(shù)為 =0.1, =1.17(表 1.29-2),故實際進給力為f fFk0fk0 =7601.17N=889.2Nf 由于切削時的進給力小于機床進給機構允許的進給力,故所選 =0.27mm/r 可f 用。 3)選擇車刀磨鈍標準及耐用度 根據(jù)表 1.9,車刀后刀面最大磨損量取為 1mm,可轉位車刀耐用度 T=30min。 4)確定切削速度 切削速度 可根據(jù)公式計算,也可直接由表中查出?,F(xiàn)采用查表法確定切削 速度。 根據(jù)表 1.10,當用 YT15 硬質(zhì)合金車刀加工鑄件, 3mm, 0.25mm/r,paf 切削速度 =450m/min。 切削速度的修正系數(shù)為 =0.8, =0.65, =0.81, =1.15, = =1.0svktvrvkvTvkM (均見表 1.28),故 =450 0.8 0.65 0.81 1.15m/min218m/min 448r/minmin/152801rdn 按 C620-1 機床的轉速(表 4.2-8),選擇 =460r/min 則實際切削速度 =218m/min 5)校驗機床功率 14 由表 1.24, 3mm, 0.27mm/r, 46m/min 時, =1.7KW。pafcP 切削功率的修正系數(shù) =1.17, , =1.13, =0.8, =0.65(表 1.28),crpk 0.10KPcMprkkc TPckckSPctpk 故實際切削時的功率為 =0.72KW 根據(jù)表 1.30,當 =460r/min 時,機床主軸允許功率 =5.9KW。 < ,故nEcPE 所選的切削用量可在 C620-1 機床上進行。 最后決定的切削用量為 =2.5mm, =0.27mm/r, =460r/min, =218m/minpafn 2、確定粗車 155 下端面的基本時間 ,ifnLj3T321lld 式中 =17.5mm, =2.5mm, =4mm, =0mm, =0.27mm/r, =460r/min, =1l1l2l3lfni 則 mi194.0in4607.53 j 工步二:粗車 73 孔的基本時間 ,ifnLj3T321ll 式中 =94mm, =1.5mm, =4mm, =0mm, =0.27mm/r, =460r/min, =1l1l2l3lfni 則 mi802.in14607.593 j 工步三:粗車 73 孔至 89 的基本時間 ,ifnLj3T321ll 式中 =63mm, =4.0mm, =4mm, =0mm, =0.27mm/r, =460r/min, =1l1l2l3lfni 則 mi143.in4607.3 j 工步四:半精車 89 孔至 89.8 的基本時間 1、 =0.4mmpa 2、 =0.15mm/rf 15 3、 =600 0.8 0.65 0.81 1.15m/min290.7m/min =600r/minn 4、確定基本工時 ,ifnLj3Tfnll321 式中 =63m, =0.4mm, =0mm, =0mm, =0.15mm/r, =600r/min, =1l1l2l3lfni 則 mi705.i6015.43j 工序 04:以 90 孔作為定位基準,粗車 155 上端面、100 端面、100 外圓、80 沉孔 、半精車 155 上端面、100 外圓、精車 100 外圓、潔角 工步一:粗車 155 上端面的基本時間 ,ifnLj3T321lld 式中 =26mm, =2.0mm, =4mm, =0mm, =0.27mm/r, =460r/min, =1l1l2l3lfni 則 mi258.0in1467.03 j 工步二:粗車 100 端面的基本時間 ,ifnLj3T321lld 式中 =15mm, =2.0mm, =4mm, =0mm, =0.27mm/r, =460r/min, =1l1l2l3lfni 則 mi170.in4607.53 j 工步三:粗車 103 外圓至 101 外圓的基本時間 ,ifnLj3Tfnll321 式中 =19.5mm, =1.0mm, =4mm, =0mm, =0.27mm/r, =460r/min, =1l1l2l3lfni 則 mi198.0in4607.593 j 工步四:粗車 80 沉孔的基本時間 16 ,ifnLj3Tfnll321 式中 =15mm, =3.5mm, =4mm, =0mm, =0.27mm/r, =460r/min, =1l1l2l3lfni 則 mi182.0i467.053 j 工步五:半精車 155 上端面的基本時間 ,ifnLj3T321lld 式中 =27mm, =0.4mm, =4mm, =0mm, =0.15mm/r, =600r/min, =1l1l2l3lfni 則 mi49.0in1605.473 j 工步六:半精車 101 外圓至 100.2 外圓的基本時間 ,ifnLj3Tfnll321 式中 =20mm, =0.4mm, =4mm, =0mm, =0.15mm/r, =600r/min, =1l1l2l3lfni 則 mi27.0i1605.43 j 工步七:精車 100.2 外圓至 100 外圓的基本時間 1、 =0.1mmpa 2、 =0.1mm/rf 3、 =800 0.8 0.65 0.81 1.15m/min387.6m/min =760r/minn 4、確定基本工時 ,ifnLj3Tfnll321 式中 =20m, =0.1mm, =0mm, =0mm, =0.1mm/r, =760r/min, =1l1l2l3lfni 則 mi265.0i761.03j 工步八:潔角 17 工序 05:以 155 外圓作為定位基準,精車 90 孔、車槽 工步一:精車 89.8 孔至 90 孔的基本時間 ,ifnLj3Tfnll321 式中 =63mm, =0.1mm, =4mm, =0mm, =0.1mm/r, =760r/min, =1l1l2l3lfni 則 mi83.0i1760.43 j 工步二:車槽 工序 06:以 90 孔作為定位基準,粗車 82 端面、52 孔、半精車、精車 52 孔 工步一:粗車 82 端面的基本時間 ,ifnLj3T321lld 式中 =16.5mm, =2.0mm, =4mm, =0mm, =0.27mm/r, =460r/min, =1l1l2l3lfni 則 mi182.0in4607.53 j 工步二:粗車 49 孔至 51 外圓的基本時間 ,ifnLj3Tfnll321 式中 =59mm, =1.0mm, =4mm, =0mm, =0.27mm/r, =460r/min, =1l1l2l3lfni 則 mi516.0in467.059T3 j 工步三:半精車 51 孔至 51.8 外圓的基本時間 ,ifnLj3fnll321 式中 =59mm, =0.4mm, =4mm, =0mm, =0.15mm/r, =600r/min, =1l1l2l3lfni 則 mi705.i1605.49T3 j 工步四:精車 51.8 孔至 512 外圓的基本時間 18 ,ifnLj3Tfnll321 式中 =59mm, =0.1mm, =4mm, =0mm, =0.1mm/r, =760r/min, =1l1l2l3lfni 則 mi81.0i760.41593 j 工序 07:以 90 孔作為定位基準,鉆 4-M8 螺紋底孔 6.8 深 21、攻 4-M8 深 18 螺紋 工步一:4-M8 螺紋底孔 6.8 深 21 選用 高速鋼錐柄麻花鉆(工藝表 3.16)m8.6 由切削表 2.7 和工藝表 4.216 查得 rmf/25.0機 (切削表 2.15)in/12v 562r/minin/8.6120rD 按機床選取 n=500r/min mi/7.051dvw 切削工時: , , 則機動工時為l21l432l03in781.i5.031 ifnltwm 工步二:攻 4-M8 深 18 螺紋 選擇 M8mm 高速鋼機用絲錐 等于工件螺紋的螺距 ,即 f=0.6mm/rf p7.5/incVm機 299r/minin/85.710rDvn 按機床選取 n=315r/min 切削工時: , , 則機動工時為l1ml6.02l03 in94.i.3582 ifnltwm 工序 08:以 90 孔作為定位基準,鉆 M3 螺紋底孔 2.55 深 8、攻 M3 深 6 螺紋 工步一:鉆 M3 螺紋底孔 2.55 深 8 19 選用 高速鋼錐柄麻花鉆(工藝表 3.16)m5.2 由切削表 2.7 和工藝表 4.216 查得 0.28/fmr機 (切削表 2.15)in/4v 500r/minin/5.2410rD 按機床選取 n=545r/min mi/.dvw 切削工時: , , 則機動工時為l81l2751l03in61.i.05432 ifnltwm 工步二:攻 M3 深 6 螺紋 選擇 M3mm 高速鋼機用絲錐 等于工件螺紋的螺距 ,即 f=0.225mm/rf pin/0.3mc機 318r/mini/1rDvn 按機床選取 n=272r/min 切削工時: , , 則機動工時為l61ml25.0l03 in12.i.732 ifnltwm 工序 09:以 90 孔作為定位基準,鉆 3-M6 螺紋底孔 5.1 深 15、攻 M6 深 12 螺紋 工步一:鉆 3-M6 螺紋底孔 5.1 深 15 選用 高速鋼錐柄麻花鉆(工藝表 3.16)m1.5 由切削表 2.7 和工藝表 4.216 查得 rmf/25.0機 (切削表 2.15)in/8v 500r/minin/1.5801rD 按機床選取 n=500r/min mi/.dvw 切削工時: , , 則機動工時為l15l52l3 20 min49.0i325.01321 ifnlltwm 工步二:攻 M6 深 12 螺紋 選擇 M6mm 高速鋼機用絲錐 等于工件螺紋的螺距 ,即 f=0.45mm/rf p7.5/mincV機 398r/minin/65.710rDvn 按機床選取 n=400r/min 切削工時: , , 則機動工時為l21ml4.02l3in258.i35.32 ifnltwm 工序 10:以 73 孔作為定位基準,鉆 4-M5 螺紋底孔 4.25 深 15、攻 M5 深 12 螺紋 工步一:鉆 4-M5 螺紋底孔 4.25 深 15 選用 高速鋼錐柄麻花鉆(工藝表 3.16)m25.4 由切削表 2.7 和工藝表 4.216 查得 rmf/25.0機 (切削表 2.15)in/7v 525r/minin/25.4710rD 按機床選取 n=500r/min mi/.610.dnvw 切削工時: , , 則機動工時為l5l254l03in61.i.0321 ifnltwm 工步二:攻 M5 深 12 螺紋 選擇 M5mm 高速鋼機用絲錐 等于工件螺紋的螺距 ,即 f=0.375mm/rf pmin/0.6CV機 21 382r/minmin/50.610rDvn 按機床選取 n=400r/min 切削工時: , ,l21l375.2ml03 則機動工時為 in41.i375.04321 ifnlltwm 工序 11:以 90 孔作為定位基準,配作 2-8 錐孔 選用 高速鋼錐柄麻花鉆(工藝表 3.16)0.8 由切削表 2.7 和工藝表 4.216 查得 0.28/fmr機 (切削表 2.15)min/15v 597r/minin/8150rD 按機床選取 n=545r/min mi/7.341dvw 切削工時: , , 則機動工時為l61l02l3in26.i8.5432 ifnltwm 工序 12:鉗工去毛刺 工序 13:檢驗至圖紙要求 工序 14:包裝、入庫 22 3 專用夾具設計 為了提高勞動生產(chǎn)率,保證加工質(zhì)量,降低勞動強度,需要設計專用夾具。 有老師分配的任務,我被要求設計鉆、攻 M3 螺紋孔。 3.1 問題的提出 本夾具主要用來鉆、攻 M3 螺紋孔,精度要求不高。因此,在本道工序加工時, 主要考慮如何提高生產(chǎn)率、降低勞動強度。 3.2 定位基準的選擇 擬定加工路線的第一步是選擇定位基準。定位基準的選擇必須合理,否則將 直接影響所制定的零件加工工藝規(guī)程和最終加工出的零件質(zhì)量。基準選擇不當往 往會增加工序或使工藝路線不合理,或是使夾具設計更加困難甚至達不到零件的 加工精度(特別是位置精度)要求。因此我們應該根據(jù)零件圖的技術要求,從保 證零件的加工精度要求出發(fā),合理選擇定位基準。此零件圖沒有較高的技術要求, 也沒有較高的平行度和對稱度要求,所以我們應考慮如何提高勞動效率,降低勞 動強度,提高加工精度。由零件圖和工藝過程得,選 155 下端面及 90 孔和 82 外圓面作為定位基準。 3.3 定位元件的設計 本工序選用的定位基準為 155 下端面及 90 孔和 82 外圓面定位,所以 23 相應的夾具上的定位元件應是心軸和 A 型固定式定位銷。因此進行定位元件的設 計主要是對心軸和 A 型固定式定位銷進行設計。夾緊則是在心軸上用帶肩螺母進 行夾緊。 1、155 下端面與心軸相配合,限制三個自由度,即 X 軸轉動、Y 軸轉動和 Z 軸移動。 2、90 孔與心軸相配合,限制兩個自由度,即 X 軸移動和 Y 軸移動。 3、82 外圓面與 A 型固定式定位銷相配合,限制一個自由度,即 Z 軸轉動。 工件六個自由度被完全限制,屬于完全定位,故設計合理。 3.4 定位誤差分析 1、 基準位移誤差 Y 由于定位副的制造誤差或定位副配合同間所導致的定位基準在加工尺寸方向上最 大位置變動量,稱為基準位移誤差,用 表示。Y 工件以 155 下端面及 90 孔和 82 外圓面來定位,鉆、攻 M3 螺紋孔,如 果工件內(nèi)孔直徑與軸外圓直徑做成完全一致,做無間隙配合,即孔的中心線與軸 的中心線位置重合,則不存在因定位引起的誤差。但實際上,軸和工件內(nèi)孔都有 制造誤差,于是工件套在軸上必然會有間隙,孔的中心線與軸的中心線位置不重 合,導致這批工件的加工尺寸 H 中附加了工件定位基準變動誤差,其變動量即為 最大配合間隙。按下式計算 )(21minaxminaxYdD 式中 基準位移誤差,mm 孔的最大直徑,mmmaxD 軸的最小直徑,mmind =0.0355mmm89.64-035.21)(21minaxY )( 2、基準不重合誤差 B 加工尺寸 h 的基準是外圓柱面的母線上,但定位基準是工件圓柱孔中心線。這 種由于工序基準與定位基準不重合導致的工序基準在加工尺寸方向上的最大位置 24 變動量,稱為基準不重合誤差,用 表示?;鶞什恢睾险`差為 =BBd21 式中 基準不重合誤差,mmB 工件的最大外圓面積直徑公差,mmd =B m0175.3.021 3.5 切削力的計算與夾緊力分析 由于本道工序主要完成工藝孔的鉆孔加工,鉆削力。由切削手冊得: 鉆削力 式(3-1)6.08.2HBDfF 鉆削力矩 式(3-2)6.0.91T 式中:D=29.8 maxaxmin187491733 代入公式(3-1)和(3-2)得 0.276 22.1010.2fr N4726.896F6.0 38511T.8..1 本道工序加工工藝孔時,夾緊力方向與鉆削力方向相同。因此進行夾緊立計 算無太大意義。只需定位夾緊部件的銷釘強度、剛度適當即能滿足加工要求。 3.6 鉆套設計 M3 螺紋加工需鉆、攻,為了我們鉆后及時攻,故選用快換鉆套(其結構如下 圖所示)以減少更換鉆套的輔助時間。根據(jù)工藝要求:。即先用 2.55 的麻花鉆 鉆孔。查機床夾具標準件可知 2.55 相配的快換鉆套的具體結構如下 具體的尺寸如下: 25 因為快換鉆套和夾具體是間隙配合,加工的時間快換鉆套靠壓緊螺釘把他壓 緊在鉆模板上,以防止加工的時間工件的旋轉,有上圖可知和快換鉆套相配的螺 釘?shù)某叽鐬?M5,查機床夾具標準件可知,M5 快換鉆套壓緊螺釘?shù)木唧w結構如下 具體的尺寸如下 26 3.7 夾具設計及操作簡要說明 如前所述,在設計夾具時,應該注意提高勞動生產(chǎn)率避免干涉。應使夾 具結構簡單,便于操作,降低成本。提高夾具性價比。本道工序為鉆床夾具 選擇由心軸、快換墊圈和帶肩螺母組成夾緊機構夾緊工件。本工序為鉆削余 量小,鉆削力小,所以一般的手動夾緊就能達到本工序的要求。 結束語 本設計中是對錐齒輪座加工工藝的編制和專用夾具的設計,使對零件的加工 過程和夾具的設計有進一步的提高。在這次的設計中也遇到了不少的問題,如在 編寫加工工藝時,對所需加工面的先后順序編排,對零件的加工精度和勞動生產(chǎn) 率都有相當大的影響。在對某幾個工序進行專用夾具設計時,對零件的定位面的 選擇,采用什么方式定位,夾緊方式及夾緊力方向的確定等等都存在問題。這些 問題都直接影響到零件的加工精度和勞動生產(chǎn)率,為達到零件能在保證精度的前 提下進行加工,而且方便快速,以提高勞動生產(chǎn)率,降低成本的目的。通過不懈 努力和指導老師的精心指導下,針對這些問題查閱了大量的相關資料。最后,將 這些問題一一解決。 27 通過做這次的設計,使對專業(yè)知識和技能有了進一步的提高,為以后從事本 專業(yè)技術的工作打下了堅實的基礎。 謝 辭 這次設計使我收益不小,為我今后的學習和工作打下了堅實和良好的基礎。 但是,查閱資料尤其是在查閱切削用量手冊時,數(shù)據(jù)存在大量的重復和重疊,由 于經(jīng)驗不足,在選取數(shù)據(jù)上存在一些問題,不過我的指導老師每次都很有耐心地 幫我提出寶貴的意見,在我遇到難題時給我指明了方向,最終我很順利的完成了 畢業(yè)設計。 這次設計成績的取得,與指導老師的細心指導是分不開的。在此,我衷