畢業(yè)設(shè)計(論文)-中間支架塑件的工藝分析以及其注射模具的設(shè)計.doc
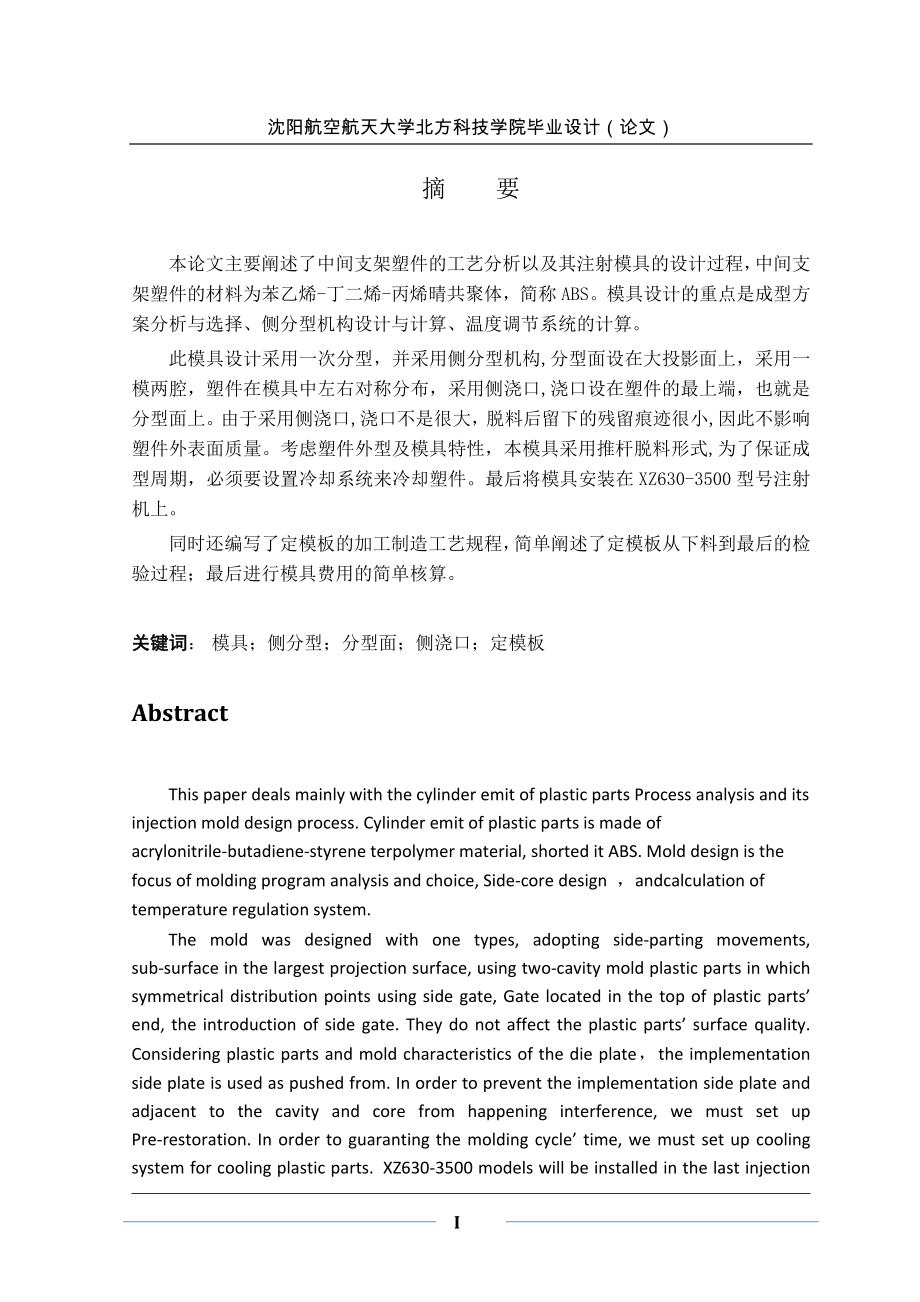


《畢業(yè)設(shè)計(論文)-中間支架塑件的工藝分析以及其注射模具的設(shè)計.doc》由會員分享,可在線閱讀,更多相關(guān)《畢業(yè)設(shè)計(論文)-中間支架塑件的工藝分析以及其注射模具的設(shè)計.doc(69頁珍藏版)》請?jiān)谘b配圖網(wǎng)上搜索。
1、沈陽航空航天大學(xué)北方科技學(xué)院畢業(yè)設(shè)計(論文)摘 要本論文主要闡述了中間支架塑件的工藝分析以及其注射模具的設(shè)計過程,中間支架塑件的材料為苯乙烯-丁二烯-丙烯晴共聚體,簡稱ABS。模具設(shè)計的重點(diǎn)是成型方案分析與選擇、側(cè)分型機(jī)構(gòu)設(shè)計與計算、溫度調(diào)節(jié)系統(tǒng)的計算。此模具設(shè)計采用一次分型,并采用側(cè)分型機(jī)構(gòu),分型面設(shè)在大投影面上,采用一模兩腔,塑件在模具中左右對稱分布,采用側(cè)澆口,澆口設(shè)在塑件的最上端,也就是分型面上。由于采用側(cè)澆口,澆口不是很大,脫料后留下的殘留痕跡很小,因此不影響塑件外表面質(zhì)量。考慮塑件外型及模具特性,本模具采用推桿脫料形式,為了保證成型周期,必須要設(shè)置冷卻系統(tǒng)來冷卻塑件。最后將模具安裝
2、在XZ630-3500型號注射機(jī)上。同時還編寫了定模板的加工制造工藝規(guī)程,簡單闡述了定模板從下料到最后的檢驗(yàn)過程;最后進(jìn)行模具費(fèi)用的簡單核算。關(guān)鍵詞: 模具;側(cè)分型;分型面;側(cè)澆口;定模板AbstractThis paper deals mainly with the cylinder emit of plastic parts Process analysis and its injection mold design process. Cylinder emit of plastic parts is made of acrylonitrile-butadiene-styrene terp
3、olymer material, shorted it ABS. Mold design is the focus of molding program analysis and choice, Side-core design ,andcalculation of temperature regulation system.The mold was designed with one types, adopting side-parting movements, sub-surface in the largest projection surface, using two-cavity m
4、old plastic parts in which symmetrical distribution points using side gate, Gate located in the top of plastic parts end, the introduction of side gate. They do not affect the plastic parts surface quality. Considering plastic parts and mold characteristics of the die plate,the implementation side p
5、late is used as pushed from. In order to prevent the implementation side plate and adjacent to the cavity and core from happening interference, we must set up Pre-restoration. In order to guaranting the molding cycle time, we must set up cooling system for cooling plastic parts. XZ630-3500 models wi
6、ll be installed in the last injection molding machine.And also prepared a template for the processing of manufacturing processes, from simple templates will be elaborated under the expected final testing process; Finally a simple cost accounting components.Keywords: Die; Pumping core; Sub-surface; S
7、ide-point gate;Mould platen符 號 表a長度mv速度m/st溫度k系數(shù)p0壓強(qiáng)MPa效率vf流體速度m/sV體積流量密度g/粘度E彈性模量MPa雷諾數(shù)v體積s面積F力N角度或w彎矩Nmm質(zhì)量gJ熱焓量KJ/KgT時間min或sc比熱容kJ/kg 目 錄引 言11 工藝分析41.1 材料介紹41.1.1 ABS的常用特性有51.1.2 ABS注塑成型的工藝條件61.1.3 ABS主要注塑成型條件61.1.4 塑料件工藝性分析72 成型方案分析與選擇92.1 成型方案92.2 初選注射機(jī)113 成型零件設(shè)計133.1 成型零件工作尺寸計算133.1.1 塑料件尺寸分類13
8、3.1.2 工作尺寸計算143.2 成型零件結(jié)構(gòu)設(shè)計153.2.1 材料選擇153.2.2 計算型腔的壁厚154 側(cè)分型機(jī)構(gòu)設(shè)計與計算174.1 簡述174.2 側(cè)分型距離174.3 包緊力與抽撥力的計算174.4 斜導(dǎo)柱的截面尺寸的計算184.5 楔緊塊的設(shè)計204.5.1 滑塊的導(dǎo)滑部分尺寸確定204.6 滑塊的限位與定位機(jī)構(gòu):215 澆注系統(tǒng)設(shè)計2225.1 主流道的設(shè)計2235.2 分流道設(shè)計2265.3 澆口設(shè)計2275.4 定位環(huán)設(shè)計2305.5 拉料桿設(shè)計2326 溫度調(diào)節(jié)系統(tǒng)356.1 熱平衡計算356.2 湍流計算367 頂出機(jī)構(gòu)設(shè)計397.1 頂出時抱緊力計算397.2 頂
9、出距離的確定397.3 推桿的擺放位置397.4 推桿的設(shè)計:398 模具排氣與引氣系統(tǒng)418.1 排氣系統(tǒng)的作用418.2 排氣結(jié)構(gòu)設(shè)計418.3 引氣系統(tǒng)429 模具總體結(jié)構(gòu)設(shè)計439.1 模具結(jié)構(gòu)件的確定439.2 動模板厚度的計算439.3 模具的閉合高度449.4 導(dǎo)柱導(dǎo)套的選擇4410 注射機(jī)相關(guān)參數(shù)的校核4510.1 額定注射壓力的校核4510.2 鎖模力的校核4510.3 模具外形尺寸4510.4 注射量的校核4510.5 開模行程的校核4611 標(biāo)準(zhǔn)件的選擇4711.1 螺栓與螺釘4711.2 圓柱銷4711.3 彈簧4711.4 導(dǎo)柱4711.5 導(dǎo)套4812 定模板制造工
10、藝規(guī)程4913 成本核算5113.1 影響模具價格的因素5113.1.1 生產(chǎn)成本5113.1.2 供貨周期5113.1.3 市場狀況5113.1.4 技術(shù)成分的含量5113.1.5 模具壽命5113.2 模具價格簡易估算5113.2.1 經(jīng)驗(yàn)估算5113.2.2 材料價格系數(shù)法5213.2.3 模具價格的具體計算過程5214 典型三維實(shí)體圖演示5514.1 定模動模板5514.2 型腔5614.3 裝配體5615 結(jié) 論57參考文獻(xiàn)58致 謝59 VI引 言模具在汽車、拖拉機(jī)、飛機(jī)、家用電器、工程機(jī)械、動力機(jī)械、冶金、機(jī)床、兵器、儀器儀表、輕工、日用五金等制造業(yè)中,起著極為重要的作用;模具是
11、實(shí)現(xiàn)上述行業(yè)的鈑金件、鍛件、粉末冶金件、鑄件、壓鑄件、注塑件、橡膠等生產(chǎn)的重要工藝裝備。采用模具生產(chǎn)毛坯或是成品零件,是材料成形的重要方式之一,與切削加工相比,具有材料利用率高、能耗低、產(chǎn)品性能好、生產(chǎn)效率高和成本低等顯著特點(diǎn)。從20世紀(jì)80年代初期開始,工業(yè)發(fā)達(dá)國家的模具工業(yè),已經(jīng)發(fā)展成為一個獨(dú)立的工業(yè)部門。改革開放以來,中國的模具工業(yè)發(fā)展十分迅速;進(jìn)年來,一直以每年15%左右的增長迅速發(fā)展。至2006年底,中國有60000多個模具制造廠點(diǎn),從業(yè)人員100多萬;2005年中國模具工業(yè)總產(chǎn)值達(dá)470億圓人民幣,中國模具工業(yè)的技術(shù)水平取得了長足的進(jìn)步。目前,中國的模具總量僅次于日本、美國,位居世
12、界第三。國民經(jīng)濟(jì)的高速發(fā)展對模具工業(yè)提出了越來越高的要求,巨大的市場需求推動著中國模具工業(yè)更快地發(fā)展。2005年中國制造業(yè)對模具的市場需求量約為570億元人民幣,并以每年10%以上的速度增長。對于大中型、精密、復(fù)雜、長壽命模具需求的增長將遠(yuǎn)超過每年10%的增幅。特別是塑料模具的飛速發(fā)展,使整個社會受益匪淺?,F(xiàn)在塑料模具已經(jīng)成為3大模具之一,在國民經(jīng)濟(jì)中占有重要的地位。塑料制品質(zhì)量的優(yōu)劣及生產(chǎn)效率的高低,模具因素約占80%。由此可知,塑料模具的設(shè)計技術(shù)與制造水平,在一定程度上標(biāo)志著一個國家的工業(yè)發(fā)展的程度。以模具的使用角度,要求高效率、自動化、操作簡便;從模具制造的角度,要求結(jié)構(gòu)合理、制造容易、
13、成本低廉。在現(xiàn)代塑料制品生產(chǎn)中,合理的加工工藝、高效的設(shè)備、先進(jìn)的模具是必不可少的三項(xiàng)重要因素,尤其是對實(shí)現(xiàn)塑料加工工藝要求、塑料制件使用要求和造型設(shè)計起到了重要作用。高效的全自動的設(shè)備也只有裝上能自動化生產(chǎn)的模具才有可能發(fā)揮其效能,產(chǎn)品的生產(chǎn)和更新都是以模具制造和更新為前提。而成型塑料制品的模具叫做塑料模具。而對于塑料模具的要求是:能生產(chǎn)出在尺寸精度、外觀、物理性能等各方面均能滿足使用要求的優(yōu)質(zhì)制品。塑料模的功能 模具是利用其特定形狀去成型具有一定型狀和尺寸的制品的工具,按制品所采用的原料不同,成型方法不同,一般將模具分為塑料模具,金屬沖壓模具,金屬壓鑄模具,橡膠模具,玻璃模具等。因人們?nèi)粘?/p>
14、生活所用的制品和各種機(jī)械零件,在成型中多數(shù)是通過模具來制成品,所以模具制造業(yè)已成為一個大行業(yè)。在高分子材料加工領(lǐng)域中,用于塑料制品成形的模具,稱為塑料成形模具,簡稱塑料模.塑料模優(yōu)化設(shè)計,是當(dāng)代高分子材料加工領(lǐng)域中的重大課題。塑料制品已在工業(yè)、農(nóng)業(yè)、國防和日常生活等方面獲得廣泛應(yīng)用。為了生產(chǎn)這些塑料制品必須設(shè)計相應(yīng)的塑料模具。在塑料材料、制品設(shè)計及加工工藝確定以后,塑料模具設(shè)計對制品質(zhì)量與產(chǎn)量,就決定性的影響。首先,模腔形狀、流道尺寸、表面粗糙度、分型面、進(jìn)澆與排氣位置選擇、脫模方式以及定型方法的確定等,均對制品(或型材)尺寸精度形狀精度以及塑件的物理性能、內(nèi)應(yīng)力大小、表觀質(zhì)量與內(nèi)在質(zhì)量等,起
15、著十分重要的影響。其次,在塑件加工過程中,塑料模結(jié)構(gòu)的合理性,對操作的難易程度,具有重要的影響。再次,塑料模對塑件成本也有相當(dāng)大的影響,除簡易模外,一般來說制模費(fèi)用是十分昂貴的,大型塑料模更是如此?,F(xiàn)代塑料制品生產(chǎn)中,合理的加工工藝、高效的設(shè)備和先進(jìn)的模具,被譽(yù)為塑料制品成型技術(shù)的“三大支柱”。尤其是加工工藝要求、塑件使用要求、塑件外觀要求,起著無可替代的作用。高效全自動化設(shè)備,也只有裝上能自動化生產(chǎn)的模具,才能發(fā)揮其應(yīng)有的效能。此外,塑件生產(chǎn)與更新均以模具制造和更新為前提。塑料摸是塑料制品生產(chǎn)的基礎(chǔ)之深刻含意,正日益為人們理解和掌握。當(dāng)塑料制品及其成形設(shè)備被確定后,塑件質(zhì)量的優(yōu)劣及生產(chǎn)效率的
16、高低,模具因素約占80%。由此可知,推動模具技術(shù)的進(jìn)步應(yīng)是不容緩的策略。尤其大型塑料模的設(shè)計與制造水平,常棵標(biāo)志一個國家工業(yè)化的發(fā)展程度。我國塑料模現(xiàn)狀 在模具方面,我國模具總量雖已位居世界第三,但設(shè)計制造水平總體上比德、美、日、法、意等發(fā)達(dá)國家落后許多,模具商品化和標(biāo)準(zhǔn)化程度比國際水平低許多。在模具價格方面,我國比發(fā)達(dá)國家低許多,約為發(fā)達(dá)國家的1/31/5,工業(yè)發(fā)達(dá)國家將模具向我國轉(zhuǎn)移的趨勢進(jìn)一步明朗化。我國塑料模的發(fā)展迅速。塑料模的設(shè)計、制造技術(shù)、CAD技術(shù)、CAPP技術(shù),已有相當(dāng)規(guī)模的確開發(fā)和應(yīng)用。在設(shè)計技術(shù)和制造技術(shù)上與發(fā)達(dá)國家和地區(qū)差距較大,在模具材料方面,專用塑料模具鋼品種少、規(guī)格
17、不全質(zhì)量尚不穩(wěn)定。模具標(biāo)準(zhǔn)化程度不高,系列化商品化尚待規(guī)?;?;CAD、CAE、Flow Cool軟件等應(yīng)用比例不高;獨(dú)立的模具工廠少;專業(yè)與柔性化相結(jié)合尚無規(guī)劃;企業(yè)大而全居多,多屬勞動密集型企業(yè)。因此努力提高模具設(shè)計與制造水平,提高國際競爭能力,是刻不容緩的。塑料模發(fā)展趨勢:1 注射模CAD實(shí)用化;2 擠塑模CAD的開發(fā);3 壓模CAD的4塑料專用鋼材系列化;5 塑料模CAD/CAE/CAM集成化;6 塑料模標(biāo)準(zhǔn)化。1 工藝分析1.1 塑料的介紹塑料的主要成分是合成樹脂。樹脂這一名詞最初是由動植物分泌出的脂質(zhì)而得名,如松香、蟲膠等,目前樹脂是指尚未和各種添加劑混合的高聚物。樹脂約占塑料總重量
18、的40%100%。塑料的基本性能主要決定于樹脂的本性,但添加劑也起著重要作用。有些塑料基本上是由合成樹脂所組成,不含或少含添加劑,如有機(jī)玻璃、聚苯乙烯等。所謂塑料,其實(shí)它是合成樹脂中的一種,形狀跟天然樹脂中的松樹脂相似,但因又經(jīng)過化學(xué)的力量來合成,而被稱之為塑料。根據(jù)美國材料試驗(yàn)協(xié)會所下的定義,塑料乃是一種以高分子量有機(jī)物質(zhì)為主要成分的材料,它在加工完成時呈現(xiàn)固態(tài)形狀,在制造以及加工過程中,可以借流動(flow)來造型。 因此,經(jīng)由此說明我們可以得到以下幾項(xiàng)了解: 它是高分子有機(jī)化合物 它可以多種型態(tài)存在例如液體固體膠體溶液等 它可以成形(moldable) 種類繁多因?yàn)椴煌膯误w組成所以造成
19、不同之塑料 用途廣泛產(chǎn)品呈現(xiàn)多樣化 具有不同的性質(zhì) 可以用不同的加工方法(processing method ) 塑料可區(qū)分為熱固性與熱可塑性二類,前者無法重新塑造使用,后者可一再重復(fù)生產(chǎn)。塑料高分子的結(jié)構(gòu)基本有兩種類型:第一種是線型結(jié)構(gòu),具有這種結(jié)構(gòu)的高分子化合物稱為線型高分子化合物;第二種是體型結(jié)構(gòu) ,具有這種結(jié)構(gòu)的高分子化合稱為體型高分子化合物。有些高分子帶有支鏈,稱為支鏈高分子,屬于線型結(jié)構(gòu)。有些高分子雖然分子間有交聯(lián),但交聯(lián)較少,稱為網(wǎng)狀結(jié)構(gòu),屬于體型結(jié)構(gòu)。 高分子的分子結(jié)構(gòu)分類: (a)線型結(jié)構(gòu) (b)線型結(jié)構(gòu)(帶有支鏈) (c)網(wǎng)狀結(jié)構(gòu)(分子鏈間少量交聯(lián)) (d)體型結(jié)構(gòu)(分子鏈
20、間大量交聯(lián)) 兩種不同的結(jié)構(gòu),表現(xiàn)出兩種相反的性能。線型結(jié)構(gòu)(包括支鏈結(jié)構(gòu))高聚物由于有獨(dú)立的分子存在,故有彈性、可塑性,在溶劑中能溶解,加熱能熔融,硬度和脆性較小的特點(diǎn)。體型結(jié)構(gòu)高聚物由于沒有獨(dú)立的大分子存在,故沒有彈性和可塑性,不能溶解和熔融,只能溶脹,硬度和脆性較大。塑料則兩種結(jié)構(gòu)的高分子都有,由線型高分子制成的是熱塑性塑料,由體型高分子制成的是熱固性塑料。 塑料主要特性:大多數(shù)塑料質(zhì)輕,化學(xué)性穩(wěn)定,不會銹蝕;耐沖擊性好;具有較好的透明性和耐磨耗性;絕緣性好,導(dǎo)熱性低;一般成型性、著色性好,加工成本低;大部分塑料耐熱性差,熱膨脹率大,易燃燒;尺寸穩(wěn)定性差,容易變形;多數(shù)塑料耐低溫性差,低
21、溫下變脆;容易老化;某些塑料易溶于溶劑。 塑料可區(qū)分為熱固性與熱可塑性二類,前者無法重新塑造使用,后者可以再重復(fù)生產(chǎn)。 基本有兩種類型:第一種是線型結(jié)構(gòu),具有這種結(jié)構(gòu)的高分子化合物稱為線型高分子化合物;第二種是體型結(jié)構(gòu),具有這種結(jié)構(gòu)的高分子化合稱為體型高分子化合物。有些高分子帶有支鏈,稱為支鏈高分子,屬于線型結(jié)構(gòu)。有些高分子雖然分子間有交聯(lián),但交聯(lián)較少,稱為網(wǎng)狀結(jié)構(gòu),屬于體型結(jié)構(gòu)。 兩種不同的結(jié)構(gòu),表現(xiàn)出兩種相反的性能。線型結(jié)構(gòu)(包括支鏈結(jié)構(gòu))高聚物由于有獨(dú)立的分子存在,故有彈性、可塑性,在溶劑中能溶解,加熱能熔融,硬度和脆性較小的特點(diǎn)。體型結(jié)構(gòu)高聚物由于沒有獨(dú)立的大分子存在,所以沒有彈性和可
22、塑性,不能溶解和熔融,只能溶脹,硬度和脆性較大。塑料則兩種結(jié)構(gòu)的高分子都有,由線型高分子制成的是熱塑性塑料,由體型高分子制成的是熱固性塑料。塑料與其它材料比較1、大部分塑料的抗腐蝕能力強(qiáng),不與酸、堿反應(yīng)。 2、塑料制造成本低。3、耐用、防水、質(zhì)輕。4、容易被塑制成不同形狀。 5、是良好的絕緣體。 6、塑料可以用于制備燃料油和燃料氣,這樣可以降低原油消耗。 塑料的缺點(diǎn):1、回收利用廢棄塑料時,分類十分困難,而且經(jīng)濟(jì)上不合算。 2、塑料容易燃燒,燃燒時產(chǎn)生有毒氣體。例如聚苯乙烯燃燒時產(chǎn)生甲苯,這種物質(zhì)少量會導(dǎo)致失明,吸入有嘔吐等癥狀,PVC燃燒也會產(chǎn)生氯化氫有毒氣體,除了燃燒,就是高溫環(huán)境,會導(dǎo)致
23、塑料分解出有毒成分,例如苯環(huán)等。3、塑料是由石油煉制的產(chǎn)品制成的,石油資源是有限的。4、塑料無法被自然分解。 1.1.1 ABS的常用特性有化學(xué)名稱:丙烯腈-丁二烯-苯乙烯共聚物,英文名稱:Acrylonitrile Butadiene Styrene,比重:1.05克/立方厘米,成型收縮率:0.40.7%,成型溫度:200240,干燥條件:80902小時。特點(diǎn):(1)綜合性能較好,沖擊強(qiáng)度較高,化學(xué)穩(wěn)定性,電性能良好。(2)與372有機(jī)玻璃的熔接性良好,制成雙色塑件,且可表面鍍鉻,噴漆處理。(3)有高抗沖、高耐熱、阻燃、增強(qiáng)、透明等級別。(4)流動性比HIPS差一點(diǎn),比PMMA、PC等好,柔
24、韌性好。ABS工程塑料一般是不透明的,外觀呈淺象牙色、無毒、無味,兼有韌、硬、剛的特性,燃燒緩慢,火焰呈黃色,有黑煙,燃燒后塑料軟化、燒焦,發(fā)出特殊的肉桂氣味,但無熔融滴落現(xiàn)象。ABS工程塑料具有優(yōu)良的綜合性能,有極好的沖擊強(qiáng)度、尺寸穩(wěn)定性好、電性能、耐磨性、抗化學(xué)藥品性、染色性,成型加工和機(jī)械加工較好。ABS樹脂耐水、無機(jī)鹽、堿和酸類,不溶于大部分醇類和烴類溶劑,而容易溶于醛、酮、酯和某些氯代烴中。1.1.2 ABS注塑成型的工藝條件成型特性:(1)無定形料,流動性中等,吸濕大,必須充分干燥,表面要求光澤的塑件須長時間預(yù)熱干燥8090度,3小時。 (2)宜取高料溫,高模溫,但料溫過高易分解(
25、分解溫度為270度).對精度較高的塑件,模溫宜取5060度,對高光澤.耐熱塑件,模溫宜取6080度。 (3)如需解決夾水紋,需提高材料的流動性,采取高料溫、高模溫,或者改變?nèi)胨坏确椒ā?(4)如成形耐熱級或阻燃級材料,生產(chǎn)37天后模具表面會殘存塑料分解物,導(dǎo)致模具表面發(fā)亮,需對模具及時進(jìn)行清理,同時模具表面需增加排氣位置。1.1.3 ABS主要注塑成型條件流動性中等,溢邊料0.04mm左右。比聚苯乙烯加工困難,宜取高料溫、模溫。料溫對物性影響很大、料溫過高易分解,對要求精度較高塑件,模溫宜去5060,要求光澤及耐熱型料宜取6080。注射壓力應(yīng)比加工聚苯乙烯稍高,一般用柱塞式注塑機(jī)時料溫為18
26、0230,注射壓力為100140Mp,螺桿式注射機(jī)則取160220Mp,70100Mp為宜。模具設(shè)計時要注意澆注系統(tǒng),選擇好進(jìn)料口位置、形式。推出力過大或機(jī)械加工時塑件表面呈“白色”。脫模斜度宜取2以上。ABS基本參數(shù)表: 表1.1 ABS基本參數(shù):密度吸水率%(24h)收縮率%成形模具溫度()料筒溫度()拉伸強(qiáng)度(MPa)1.051.061.63.00.40.7506018023070彈性模量(MPa)彎曲強(qiáng)度(MPa)沖擊強(qiáng)度(不斷無缺口)硬度體積電阻率()介質(zhì)強(qiáng)度96.911.811.6HB1.1.4 塑料件工藝性分析塑件為中間支架塑件,實(shí)體圖見圖1.1:圖1.1中間支架塑件塑件為一對稱
27、實(shí)體,側(cè)面上3個通孔,支架兩側(cè)壁厚為5mm,有2個方向分型,制件大體尺寸為704025mm。形狀較規(guī)則,外形不是很復(fù)雜,基本上都是平面所組成。從塑件圖形可以看出,此中間支架塑件結(jié)構(gòu)對稱,所以采用對稱的側(cè)分型結(jié)構(gòu),有側(cè)抽芯機(jī)構(gòu)。ABS流動性中等,主流道最好做成粗短為好,且采用側(cè)澆口。這里模具結(jié)構(gòu)采用一次分型機(jī)構(gòu),分型面取在塑件小圓柱體的端面處,一模兩腔,塑件分型面采用平直分型面,開模時側(cè)分型機(jī)構(gòu)隨模具同時進(jìn)行運(yùn)動,最后采用推桿脫模機(jī)構(gòu)將塑件脫模。2 成型方案分析與選擇根據(jù)塑料制件圖可以看出,由于塑料件本身形狀特點(diǎn),塑料件的分型面只有一種,是第一章1.2節(jié)中論述的方案一中把分型面設(shè)在塑件的頂端平面
28、上。除此若把分型面設(shè)在其它面上,將會導(dǎo)致塑料外形有缺陷。2.1 成型方案1、方案一:模具采用一模兩腔、一次分型。模具采用斜導(dǎo)柱側(cè)分型機(jī)構(gòu),澆口形式采用側(cè)澆口,脫模采用推桿式脫模機(jī)構(gòu)將塑件脫模。如圖2.1所示:1導(dǎo)套,2導(dǎo)柱,3定模座板,4冷卻水道,5內(nèi)六角螺釘,6定位環(huán),7澆口套8靜模型芯,9動模型芯,10定模板,11銷釘,12螺釘,13動模板,14動模墊板,15支撐塊,16銷釘,17螺釘,18動模座板,19螺釘,20推板,21推桿,22推桿,23銷釘,24拉料桿,25推板固定板,26螺釘,27限位擋塊,28 彈簧,29銷釘,30螺釘,31滑塊,32斜導(dǎo)柱,33楔緊塊,34導(dǎo)套,35導(dǎo)柱,36
29、復(fù)位桿,37水嘴圖2.1 方案一草圖(一模兩腔)l 方案二:模具采用一模二腔,一次分型。模具和方案一沒有大的區(qū)別,采用側(cè)澆口,脫模采用推桿脫模機(jī)構(gòu),同樣也要設(shè)側(cè)分型機(jī)構(gòu),但是塑件在模具中的位置和方案一中的垂直。表2.1 成型方案優(yōu)缺點(diǎn)分析成型方案優(yōu)點(diǎn)缺點(diǎn)方案一(一模兩腔)1 采用側(cè)澆口,可以根據(jù)塑件的形狀特征靈活地選擇進(jìn)料位置,對各種塑料的成型適應(yīng)性均較強(qiáng);2 采用左、右兩個方向抽芯;3 模具結(jié)構(gòu)受力對稱,均勻,模具不易磨損,一模兩腔效率高,適于大批量生產(chǎn);4 主流道短,塑件熔料不宜凝固。1. 采用側(cè)澆口,有澆口痕跡存在,會形成熔接痕、縮孔、氣孔等塑件缺陷;2. 側(cè)澆口存在壓力損失大的問題。方
30、案二(一模兩腔)1 模具采用側(cè)澆口,澆口易加工,修模方便;2 一模兩腔,生產(chǎn)效率高,適合生產(chǎn)批量較大場合;1. 側(cè)澆口會留下殘留痕跡,影響塑件表面質(zhì)量;2. 側(cè)澆口會形成熔接痕,縮孔,氣孔等塑件缺陷,且注塑壓力損失大,對深型腔塑件排氣不便 。3.內(nèi)抽芯導(dǎo)致模具結(jié)構(gòu)復(fù)雜。 綜合考慮兩種成型方案的優(yōu)缺點(diǎn),在根據(jù)塑料制件的生產(chǎn)批量較大,可以得出結(jié)論方案一最好,故這里選取方案一(一模二腔)來生產(chǎn)中間支架塑件。2.2 初選注射機(jī)成型方案選定之后就要選擇注射機(jī),在這里計算塑料體積然后先初選注射機(jī),塑料制件外形不是很規(guī)則,用CATIA軟件做出零件實(shí)體圖,得到其體積為:V=1.375x總質(zhì)量:m=v=1.05
31、xkg/x1.375x=0.144kg=144g由CATIA軟件可計算出塑料制件的體積約為1.375,采用一模兩腔,考慮到還有主澆道、分澆道,冷料穴等部分,塑料制件的體積應(yīng)在注射機(jī)額定注射量的15%80%左右比較合適,故先根據(jù)注射量選用SZ-630/3500型號注射機(jī)。其相關(guān)參數(shù)見下頁表2.2: 表2.2 SZ630/3500注射機(jī)參數(shù)螺桿直徑58mm機(jī)器外形470010001815額定注射量634定位環(huán)尺寸175mm注射壓力150Mpa動定模固定板尺寸598520注射行程150mm噴嘴圓弧半徑18 mm最大開合模行程490mm噴嘴孔直徑5mm最大成型面積750鎖模力3500KN模具最小厚度2
32、50mm拉桿空間545485模具最大厚度500mm合模方式增壓式3 成型零件設(shè)計3.1 成型零件工作尺寸計算這里的公差按自由尺寸級給出。 3.1.1 塑料件尺寸分類圖3.1 塑件尺寸分類孔類尺寸(A類):A1=3mm A2=5mmA3=70mm A4=9mmA5=5mm軸類尺寸(B類): B1=30mm B2=15mm中心類尺寸(C類):C1=16mm C2=17mmC3=6mm C4=30mmC5=44mm 3.1.2 工作尺寸計算 由手冊中查得ABS材料的成型收縮率為0.4%0.7%,這里取收縮率為平均收縮率=0.55%,取模具制造精度為IT7級;由于制品尺寸不大,在計算時型心尺寸修正系數(shù)
33、x取3/4,計算高度和深度尺寸時,x取2/3。將型心各工作尺寸的制造公差按制品公差的1/3取值??最惓叽纾ˋ類)(依據(jù)塑件對應(yīng)孔徑向尺寸計算,塑件精度按4級取值):由公式: (3.1)公式中:為塑料件公差,把各尺寸代入公式(3.1)得如下:mmmm mmmmmm 軸類尺寸(B類):由公式: (3.2)把各尺寸代入公式(3.3)得如下:mmmm 中心類尺寸(C類):由公式: (3.3)把各尺寸代入公式(3.4)得如下:mmmmmmmmmm模具上各成型零件的成型尺寸依據(jù)上述計算出來的對應(yīng)尺寸給出??紤]到便于脫模要加脫模斜度,查閱資料得出ABS材料:型腔脫模斜度為;型芯脫模斜度為 曹宏深 趙仲治主編
34、 塑料成型工藝與模具設(shè)計 機(jī)械工業(yè)出版社 1993年 134頁表5-8塑料制品常用脫模斜度考慮到制品深度較大時,脫模斜度應(yīng)選較小值,反之可選較大值,型腔脫模斜度可以比型芯小一些。此畢設(shè)塑件尺寸不大,精度為自由級,精度不高,由于模具采用側(cè)分型,故型腔可不必設(shè)脫模斜度。綜合考慮這里取型腔脫模斜度為0,型芯脫模斜度為。斜度由縮小方向取得。3.2 成型零件結(jié)構(gòu)設(shè)計3.2.1 材料選擇適合于ABS材料成型的鋼材有40Cr,供貨硬度為40HRC,易于切削加工。而后在真空環(huán)境下經(jīng)500C550C,以510h時效處理,鋼材彌散析出復(fù)合合金化合物,使剛才硬度具有HRC4045的硬度,耐磨性好且變形小。由于材質(zhì)純
35、凈,可做鏡面拋光,并能光腐蝕精細(xì)圖案,有較好的電加工及抗銹蝕性能。工作溫度可達(dá)300C,抗拉強(qiáng)度為1400Mpa。還有SM2(20CrNi3AlMnMo),預(yù)硬化后機(jī)加工,再經(jīng)時效硬化可以達(dá)到4045HRC。這里考慮材料應(yīng)易于拋光,這樣才能使塑料件易于脫模,且兩種鋼性能相近,都是析出硬化鋼。故這里選取40Cr作為成型零件材料。3.2.2 計算型腔的壁厚在設(shè)計模具,決定成型零件尺寸時,必須考慮強(qiáng)度,在實(shí)際生產(chǎn)中,注射模具經(jīng)常由于??蚣爸伟搴穸炔粔蛞饛椥宰冃?影響塑料制件尺寸精度或溢料過多,費(fèi)邊增加,為了增加模具強(qiáng)度與剛性,如果把??蚝桶寄1诤褚约皦|板等的厚度無原則的放大,則不但浪費(fèi)模具材料,
36、而且模具笨重,操作費(fèi)力,因此設(shè)計時應(yīng)加以合理的計算.型腔壁厚計算以最大壓力為準(zhǔn),理論分析和實(shí)踐證明,對于大尺寸的型腔,剛度不足是主要矛盾,應(yīng)按剛度計算,而小尺寸的型腔在發(fā)生大的彈性變形前,其內(nèi)應(yīng)力往往就超過了許用應(yīng)力,因此按強(qiáng)度計算.這里的中間支架塑件尺寸不是很大,故按小尺寸型腔計算,即按強(qiáng)度計算。在此把模具型腔簡化為一個組合式圓形型腔:則用r表示組合型腔腔內(nèi)尺寸,30 x25;用h表示組合型腔高度,h=45mm。組合圓形型腔側(cè)壁壁厚計算公式: (3.6)凹模墊板厚度計算公式: (3.7)公式中: 表示模具鋼的允許強(qiáng)度值,因?yàn)?0Cr為預(yù)硬化鋼,故取=300MPaP表示模具最大型腔成型壓力,這
37、里取P=50Mpa代入數(shù)據(jù)得:型芯側(cè)壁壁厚 S=9.6mm型腔底板或凸模支撐板厚度 T=27.1mm實(shí)際模具中的取值比以上計算值大些就可以了。4 側(cè)分型機(jī)構(gòu)設(shè)計與計算4.1 簡述在成型有側(cè)孔,側(cè)凹或者有些凸臺的塑件時,通常采用側(cè)向分型方法將成型側(cè)孔,側(cè)凹或者側(cè)凸臺的部位做成側(cè)型芯或側(cè)型腔,在塑件脫模前先將側(cè)型芯或側(cè)型腔抽出,然后再從模具中頂出塑件。能將側(cè)型芯或側(cè)型腔抽出和復(fù)位的機(jī)構(gòu)叫側(cè)向分型與抽芯機(jī)構(gòu)。4.2 側(cè)分型距離抽芯距離S是將活動型芯(側(cè)向型芯或瓣合模塊)從成型位置抽至不妨礙塑件脫模位置所移動的距離。為安全起見,抽芯距通常比側(cè)孔或側(cè)凹的深度大23mm,但是在活動型芯脫出側(cè)孔或側(cè)凹后,其
38、幾何位置有礙于塑件脫模的情況下,抽芯距不能簡單的按照這種方法確定。而本塑件側(cè)孔的深度為5mm,所以模具的側(cè)向抽芯的距離為8mm.4.3 包緊力與抽撥力的計算注射成型后,塑料制件在模具內(nèi)冷卻定型,由于體積的收縮,對型芯產(chǎn)生包緊力,塑件要在模腔中脫出就必須要克服包緊力,同時要產(chǎn)生摩擦阻力。對于不帶通孔的殼體類塑件,脫模時還要克服大氣壓力。 將側(cè)向活動型芯從塑件中抽出所需的力叫抽拔力,其計算同脫模力的計算,也可按如下的簡要公式計算: (4.2) 式中,是活動型心被塑件包圍的斷面形狀周長(mm),是成型部分的深度(mm),是側(cè)孔或側(cè)凹的脫模斜度(),是塑件對型心單位面積的擠壓力,一般取812,是塑料與
39、鋼的摩擦系數(shù),一般取0.10.2。A為塑件包容型芯的表面積,由單個塑件計算出塑件對定模一側(cè)的型心的包緊表面積為:= n為側(cè)型心的個數(shù),d是側(cè)孔的直徑,h是側(cè)孔的深度=33.1475=329.7N4.4 斜導(dǎo)柱的截面尺寸的計算本模具左右滑塊采用斜導(dǎo)柱導(dǎo)向,故計算滑塊導(dǎo)柱的截面尺寸。斜導(dǎo)柱工作時主要受彎矩作用,斜導(dǎo)柱的截面尺寸應(yīng)按彎曲強(qiáng)度條件進(jìn)行設(shè)計。而彎矩取決于抽拔力和斜導(dǎo)柱的斜角以及斜導(dǎo)柱的工作長度,斜導(dǎo)柱的最大彎矩M可能出現(xiàn)在開模初始,因?yàn)榇藭r的抽拔力最大;隨著開模行程的加大,抽拔力會迅速減小,但是力臂要增加,特別是斜導(dǎo)柱工作部分長度L較長時,最大彎矩也可能出現(xiàn)在與滑塊即將分離時,因此嚴(yán)格來
40、說應(yīng)選兩者的較大者進(jìn)行計算分析;但是本模具側(cè)分型距離不長,斜導(dǎo)柱也不是很長,且由于隨著開模過程的進(jìn)行,側(cè)分型力是要迅速下降而不是慢慢減小的,力臂的增加是非常有限的,故最大彎矩一定出現(xiàn)在開模開始的瞬間,所以只要按開模時的彎矩進(jìn)行計算肯定能滿足強(qiáng)度要求。M= (4.3)式中:F 為斜導(dǎo)柱承受的最大彎曲力,(N)為彎曲力作用點(diǎn)距離斜導(dǎo)柱伸出部分跟部的距離,(m)又由材料力學(xué)分析可以得到:M=W (4.4)式中: 為斜導(dǎo)柱所用材料的許用彎曲應(yīng)力,這里選取硬度在HRC5458的T10鋼,=155Pa;W為抗彎截面系數(shù),對于截面為圓形的斜導(dǎo)柱,W=0.1。所以斜導(dǎo)柱的直徑為:d= = (4.5)式中:為滑
41、塊受的脫模力作用線與斜導(dǎo)柱中心線的交點(diǎn)到斜導(dǎo)柱固定的距離,m。為30mm即0.03m即為上節(jié)中的=329.7N=155Paa為斜導(dǎo)柱斜角,這里取a=則斜導(dǎo)柱的直徑為:=0.0117m=11.7mm取d=15mm。這里采用圓形斜導(dǎo)柱:斜導(dǎo)柱如圖4.1所示 圖4.1斜導(dǎo)柱如圖4.2所示,斜角為a=20,抽芯距離S=5mm,定模板厚度h=25,斜導(dǎo)柱直徑d=15mm,斜導(dǎo)柱臺階直徑D=20mm;為了防止在分型時發(fā)生卡死現(xiàn)象,這里將滑塊上的斜導(dǎo)柱孔的最大尺寸取為15+0.5=15.5mm,以后都以15.5mm計算。 =3.6mm=21.3mm = =2.7mm=58.2mm=5mm則斜導(dǎo)柱總長L=+=
42、13.6+21.3+2.7+58.2+5=90mm故L=90mm。4.5 楔緊塊的設(shè)計楔緊塊設(shè)計,參照圖4.2:圖4.2楔緊塊設(shè)計示意圖斜導(dǎo)柱的傾斜角為,為讓楔緊塊在開模時能不影響滑塊的運(yùn)行,楔緊面的傾斜角要比斜導(dǎo)柱的傾斜角大,這里取為,楔緊面深H=24mm,寬取90mm。楔緊塊按過贏配合固定在定模座板上,可以滿足強(qiáng)度要求。防止因強(qiáng)度不足而發(fā)生破壞。4.5.1 滑塊的導(dǎo)滑部分尺寸確定這里考慮導(dǎo)滑部分不承受力的作用,即使有力的作用也不是很大,故尺寸不需太大且也不用計算校核。這里給出導(dǎo)滑槽尺寸為10mm5mm(10mm為滑槽的高)。圖4.3滑塊 59沈陽航空航天大學(xué)北方科技學(xué)院畢業(yè)設(shè)計(論文)4.
43、6 滑塊的限位與定位機(jī)構(gòu):此模具的滑塊和型腔是一體的,全部包在型心底板里面,導(dǎo)滑的方向和模具的軸線是垂直的,只要保證滑塊運(yùn)動到設(shè)計要求的位置時不從型心底板里面脫出來,同時也能在指定的位置上定位即可。所以只要使用限位檔塊限位定位就可以了,其大體尺寸見圖4.4:圖4.4限位檔塊沈陽航空航天大學(xué)北方科技學(xué)院畢業(yè)設(shè)計(論文)4.7分型面的設(shè)計 :分開模具取出塑件的面稱為分型面;注射模有一個分型面或多個分型面,分型面的位置,一般垂直于開模方向。分型面的形狀有平面和曲面等,但也有將分型面作傾斜的平面或彎折面,或曲面,這樣的分型面雖加工難,但型腔制造和制品脫模較易。有合模對中錐面的分型面,分型面自然也是曲面
44、。選擇分型面時,應(yīng)考慮的基本原則:1) 分型面應(yīng)選在塑件外形最大輪廓處當(dāng)已經(jīng)初步確定塑件的分型方向后分型面應(yīng)選在塑件外形最大輪廓處,即通過該方向塑件的截面積最大,否則塑件無法從形腔中脫出。2) 確定有利的留模方式,便于塑件順利脫模從制件的頂出考慮分型面要盡可能地使制件留在動模邊,當(dāng)制件的壁相當(dāng)厚但內(nèi)孔較小時,則對型芯的包緊力很少常不能確切判斷制件中留在型芯上還是在凹模內(nèi)。這時可將型芯和凹模的主要部分都設(shè)在動模邊,利用頂管脫模,當(dāng)制件的孔內(nèi)有管件(無螺紋連接)的金屬嵌中時,則不會對型芯產(chǎn)生包緊力。3) 保證制件的精度和外觀要求與分型面垂直方向的高度尺寸,若精度要求較高,或同軸度要求較高的外形或內(nèi)
45、孔,為保證其精度,應(yīng)盡可能設(shè)置在同一半模具腔內(nèi)。因分型面不可避免地要在制件中留下溢料痕跡或接合縫的痕跡,故分型面最好不選在制品光亮平滑的外表面或帶圓弧的轉(zhuǎn)角處。4) 分型面應(yīng)使模具分割成便于加工的部件,以減少機(jī)械加工的困難。5) 不妨礙制品脫模和抽芯。在安排制件在型腔中的方位時,要盡量避免與開模運(yùn)動相垂直方向的避側(cè)凹或側(cè)孔。6) 有利于澆注系統(tǒng)的合理處置。7) 盡可能與料流的末端重合,以利于排氣。本次設(shè)計產(chǎn)品的分型面在塑件上一目了然,分型面設(shè)在塑件的對稱面上如圖,所以不必再選擇,這樣的分型面必然產(chǎn)生側(cè)向抽芯,實(shí)際上也是這樣的分型面最合理。5 澆注系統(tǒng)設(shè)計5.1 主流道的設(shè)計5.1.1主流道的作
46、用主流道(也叫進(jìn)料口),它是連接注射機(jī)料筒噴嘴和注射模具的橋梁,也是熔融的塑料進(jìn)入模具型腔時最先經(jīng)過的地方。主流道的大小和塑料進(jìn)入型腔的速度及充模時間長短有著密切關(guān)系。若主流道太大,其主流道塑料體積增大,回收冷料多,冷卻時間增長,使包藏的空氣增多,如果排氣不良,易在塑料制品內(nèi)造成氣泡或組織松散等缺陷,影響塑料制品質(zhì)量,同時也易造成進(jìn)料時形成旋渦及冷卻不足,主流道外脫模困難;若主流道太小,則塑料在流動過程中的冷卻面積相應(yīng)增加,熱量損失增大,粘度提高,流動性降低,注射壓力增大,易造成塑料制品成形困難。主流道部分在成型過程中,其小端入口與注射機(jī)噴嘴及一定溫度、壓力的塑料熔要冷熱交替地反復(fù)接觸,屬易損
47、件,對材料的要求較高因而模具的主流道部分常設(shè)計成可拆卸更換的主流道襯套式(俗稱澆口套),以便有效地選用鋼材單獨(dú)進(jìn)行加工和熱處理。一般采用碳素工具鋼T8A、T10A等,熱處理要求淬火5357HRC。在一般情況下,主流道不直接開設(shè)在定模板上,而是制造成單獨(dú)的澆口套,鑲定在模板上。小型注射模具,批量生產(chǎn)不大,或者主流道方向與鎖模方向垂直的模具,一般不用澆口套,而直接開設(shè)在定模板上。澆口套是注射機(jī)噴嘴在注射模具上的座墊,在注射時它承受很大的注射機(jī)噴嘴端部的壓力同時由于澆口套末端通過流道澆口與型腔相連接,所以也承受模具型腔壓力的反作用力。為了防止?jié)部谔滓驀娮於瞬繅毫Χ粔喝肽>邇?nèi),澆口套的結(jié)構(gòu)上要增加臺
48、肩,并用螺釘緊固在模板上,這樣亦可防止模腔壓力的反作用力而把澆口套頂出。5.1.2主流道設(shè)計要點(diǎn)(1) 澆口套的內(nèi)孔(主流道)呈圓錐形,錐度2 6。若錐度過大會造成壓力減弱,流速減慢,塑料形成渦流,熔體前進(jìn)時易混進(jìn)空氣,產(chǎn)生氣孔;錐度過小,會使阻力增大,熱量損耗大,表面黏度上升,造成注射困難。(2) 澆口套進(jìn)口的直徑d應(yīng)比注射機(jī)噴嘴孔直徑d1大0.5mm。若等于或小于注射機(jī)噴嘴直徑,在注射成型時會造成死角,并積存塑料,注射壓力下降,塑料冷凝后,脫模困難。(3) 澆口套內(nèi)孔出料口處(大端)應(yīng)設(shè)計成圓角r,一般為0.53mm。(4) 澆口套與注射機(jī)噴在接觸處球面的圓弧度必須吻合。設(shè)球面澆口套球面半
49、徑為SR,注射機(jī)球面半徑為r,其關(guān)系式如下:SRr0.51mm澆口套球面半徑比注射機(jī)噴嘴球面半徑大,接觸時圓弧度吻合的好。(5) 澆口套長度(主流道長度)應(yīng)盡量短,可以減少冷料回收量,減少壓力損失和熱量損失。(6) 澆口套錐度內(nèi)壁表面粗糙度為Ra1.6Ra0.8m,保證料流順利,易脫模。(7) 澆口套不能制成拼塊結(jié)構(gòu),以免塑料進(jìn)入接縫處,造成冷料脫模困難。(8) 澆口套的長度應(yīng)與定模板厚度一致,它的端部不應(yīng)凸出在分型面上,否則會造成合模困難,不嚴(yán)密,產(chǎn)生溢料,甚至壓壞模具。(9) 澆口套部位是熱量最集中的地方,為了保證注射工藝順利進(jìn)行和塑件質(zhì)量,要考慮冷卻措施。圖5.1 澆注系統(tǒng)設(shè)計主流道設(shè)計
50、注意事項(xiàng):主澆道進(jìn)口端直徑一般比噴嘴出口直徑大mm;主澆道錐角約取,對流動性差的塑料?。恢鳚驳莱隹诙藨?yīng)有圓角,圓角半徑R約為mm或0.125倍的出口端直徑;主澆道表壁的表面粗糙度應(yīng)小于Ra0um或高于;主流道長度應(yīng)盡量短,一般小于或等于60mm;主流道進(jìn)口端與噴嘴頭部接觸處應(yīng)做成凹下的球面,以便與噴嘴頭部的球面半徑匹配,否則容易造成溢料,給推卸澆口凝料造成困難,通常要求主流道進(jìn)口端凹下的球面半徑要比噴嘴球面半徑大mm,凹下深度約為mm。由于注射成型時主流道要與高溫塑料熔料和注射機(jī)噴嘴反復(fù)接觸和碰撞,所以一般都不將主流道直接開在定模上,而是單獨(dú)將它開設(shè)在一個鑲套里,再將此嵌套嵌入定模里,該嵌套稱
51、為主流襯套,采用主流襯套后,不僅對主流道的加工帶來很大方便,而且在主流道損壞后也便于修?;蚋鼡Q。如圖5-1所示,這樣主流道襯套可用更優(yōu)質(zhì)的鋼材如T8加工和熱處理,使質(zhì)量提高,成本降低。由注射機(jī)的噴嘴孔直徑為5mm,這里取=5+1=6mm,由噴嘴圓弧半徑為18mm,這里取SR=18+2=20mm,為了便于脫模取a=,也就是每個邊與豎直方向成的夾角。主流道的外形尺寸:, , , b=mm,取b=0.5mm R=0.4mm 5.2 分流道設(shè)計分流道設(shè)計要點(diǎn):分流道長度應(yīng)保證型腔合理布局,并有足夠強(qiáng)度去除澆口方便的前提下盡量取短;分流道應(yīng)平直,盡量避免彎曲拐角,轉(zhuǎn)換方向應(yīng)圓滑平穩(wěn);多型腔時,各型腔的分
52、澆道距離盡量一致,分澆道截面應(yīng)等于或大于各進(jìn)料口各截面之和;分流道截面大小及形狀應(yīng)按塑料性能,塑件體積,壁厚,形狀復(fù)雜程度而定,一般分流道為進(jìn)料口截面1.5倍,截面常采用梯形,槽寬為槽身的1.5-2倍,槽深按塑件大小而定;多型腔時應(yīng)合理分布分澆道;分流道表壁粗糙度不宜太小,以免將冷料帶入模腔,一般達(dá)到即可;當(dāng)分流道較長時,其末端應(yīng)有冷料穴。分流道的斷面形狀尺寸:分流道截面的大小,決定于滿足良好的壓力傳遞和合理的填充時間等(既阻力小,溫度降低?。?,圓形分流道的比表面積?。ū砻娣e與其體積之比值稱比表面積),熱量不容易散失,阻力也小,但流道加工較難,且安裝后不容易保證對中。梯形分流道的熱量損失和阻力
53、也不太大,并且加工方便。半圓形分流道的比表面積大,矩形分流道的比表面積也大。這里綜合考慮到塑料制件的體積較大,對分流道的要求是盡量做到比表面積小,且要有較好的加工工藝性,所以這里選取梯形分流道,并開設(shè)在動模一側(cè)。分流道的尺寸視制品大小、塑料品種、注射速率、以及流道長度而定。實(shí)踐證明圓形截面的流道是最好的,而恰好能容納一個所需直徑整圓的梯形的截面,當(dāng)其側(cè)邊與垂直于分型面的方向成的夾角時,其流動性和傳熱性和圓形截面流道一樣好。因?yàn)樘菪畏至鞯赖谋缺砻娣e和圓形分流道的相近,故可以先選定圓形分流道的直徑,然后在把直徑轉(zhuǎn)換成相等的梯形分流道尺寸。本模具采用梯形澆道,這里免去計算,直接參照塑料模具設(shè)計手冊1
54、56頁表5.5常用澆道尺寸系列如下:表5.1常用澆道尺寸梯形截面澆道 L46(7)8(9)1012H34(5)5.5(6)78注:1.括號尺寸一般不用. 2.H=L,R一般取13mm本模具梯形分澆道截面尺寸取L=12mm,H=8mm,R=2mm,單側(cè)斜邊與垂直于分型面的方向的夾角取。5.3 澆口設(shè)計5.3.1澆口的作用澆口是分流道和型腔之間的連接部分,也是注射模具澆注系統(tǒng)的最后部分,通過澆口直接使熔融的塑料進(jìn)入型腔內(nèi)。澆口的作用是使從流道來的熔融塑料以較快的速度進(jìn)入并充滿型腔,型腔充滿塑料后,澆口能迅速冷卻封閉,防止型腔內(nèi)還未冷卻的熱料回流。澆口設(shè)計與塑料制品形狀、塑料制品斷面尺寸、模具結(jié)構(gòu)、
55、注射工藝參數(shù)(壓力等)及塑料性能等因素有關(guān)。澆口的截面要小,長度要短,這樣才能增大料流速度,快速冷卻封閉,便于使塑料制品分離,塑料制品的澆口痕跡亦不明顯。 塑料制品質(zhì)量的缺陷,如缺料、縮孔、拼縫線、質(zhì)脆、分解、白斑、翹曲等,往往都是由于澆口設(shè)計不合理而造成的。5.3.2澆口設(shè)計的基本要點(diǎn)1) 盡量縮短流動距離 澆口位置的安排應(yīng)保證塑料熔體迅速和均勻地充填模具型腔,盡量縮短熔體的流動距離,減少壓力損失,有利于排除模具型腔中的氣體,這對大型塑件更為重要。2) 澆口應(yīng)設(shè)在塑件制品斷面較厚的部位 當(dāng)塑件的壁厚相差較大時,若將澆口開設(shè)在塑件的薄壁處,這時塑料熔體進(jìn)入型腔后,不但流動阻力大,而且還易冷卻,
56、以致影響了熔體的流動距離,難以保證其充滿整個型腔。另外從補(bǔ)縮的角度考慮,塑件截面最厚的部位經(jīng)常是塑料熔體最晚固化的地方,若澆口開設(shè)在薄壁處,則厚壁處極易因液態(tài)體積收縮得不到收縮而形成表面凹陷或真空泡。因此為保證塑料熔體的充分流動性,也為了有利于壓力有效地傳遞和比較容易進(jìn)行因液態(tài)體積收縮時所需的補(bǔ)料,一般澆口的位置應(yīng)開設(shè)在塑件壁最厚處。3) 必須盡量減少或避免熔接痕 由于成型零件或澆口位置的原因,有時塑料充填型腔時造成兩股或多股熔體的匯合,匯合之處,在塑件上就形成熔接痕。熔接痕降低塑件的強(qiáng)度,并有損于外觀質(zhì)量,這在成型玻璃纖維增強(qiáng)塑料的制件時尤為嚴(yán)重。有時為了增加熔體的匯合,匯合之處,在塑件上就
57、形成熔接痕。熔接痕降低塑件的強(qiáng)度,并有損于外觀質(zhì)量,這在成型玻璃纖維增強(qiáng)塑料的制件時尤其嚴(yán)重。一般采用直接澆口、點(diǎn)澆口、環(huán)形澆口等可以避免熔接痕的產(chǎn)生,有時為了增加熔體匯合處的溶接牢度,可以在溶接處外側(cè)設(shè)一冷料穴,使前鋒冷料引如其內(nèi),以提高熔接強(qiáng)度。在選擇澆口位置時,還應(yīng)考慮熔接的方位對塑件質(zhì)量及強(qiáng)度的不同影響。4) 應(yīng)有利于型腔中氣體的排除 要避免從容易造成氣體滯留的方向開設(shè)澆口。如果這一要求不能充分滿足,在塑件上不是出現(xiàn)缺料、氣泡就是出現(xiàn)焦斑。同時熔體充填時也不順暢,雖然有時可用排氣系統(tǒng)來解決,但在選擇澆口位置時應(yīng)先行加以考慮。5) 考慮分子定向影響 充填模具型腔期間,熱塑性塑料會在流動方
58、向上2呈現(xiàn)一定的分子取向,這將影響塑件的性能。對某一塑件而言,垂直流向和平行于流向的強(qiáng)度、應(yīng)力開裂傾向等都是有差別的,一般在垂直于流向的方位上強(qiáng)度降低,容易產(chǎn)生應(yīng)力開裂。6) 避免產(chǎn)生噴射和蠕動(蛇形流) 塑料熔體的流動主要受塑件的形狀和尺寸以及澆口的位置和尺寸的支配,良好的流動將保證模具型腔的均勻充填并防止分層。塑料濺射進(jìn)入型腔可能增加表面缺陷、流線、熔體破裂及氣,如果通過一個狹窄的澆口充填一個相對較大的型腔,這種流動影響便可能出現(xiàn)。特別是在使用低粘度塑料熔體時更應(yīng)注意。通過擴(kuò)大尺寸或采用沖擊型澆口(使料流直接流向型腔壁或粗大型芯),可以防止噴射和蠕動。7) 澆口與塑件連接得部位應(yīng)成R0.5
59、的圓角或0.545的倒角;澆口和流道連接的部位一般斜度為3045,并以R1R2的圓弧和流道底面相連接。5.3.3澆口的類型澆口的形式多種多樣,但常用的澆口有如下11種:直接澆口、側(cè)澆口、扇形澆口、平縫澆口、環(huán)形澆口、盤形澆口、輪輻澆口、爪形澆口、點(diǎn)澆口、潛伏澆口、護(hù)耳澆口等。本次設(shè)計采用側(cè)澆口形式。側(cè)澆口又稱邊緣澆口,國外稱之為標(biāo)準(zhǔn)澆口。側(cè)澆口一半開設(shè)在分型面上,塑料熔體于型腔的側(cè)面充模,其截面形狀多為矩形狹縫(也有半圓型的注入口)。這類澆口加工容易,修整方便,并且可以根據(jù)素件的形狀特征靈活地選擇進(jìn)料位置,因此它是廣泛使用的澆口形式,普遍用于中小型塑件的多型腔模具,且對于各種塑料的成型適應(yīng)型較強(qiáng),這些都是本次設(shè)計采用側(cè)澆口的主要原因;但側(cè)澆口痕跡存在,會形成熔接痕、縮孔、氣孔等缺陷,且注射壓力損失大,對深型腔塑料排氣不便。這次設(shè)計的塑件允許存在熔接痕,且型腔不深,故可采用。 側(cè)澆口的尺寸按經(jīng)驗(yàn)公式計算如下:b(0.60.9)30tb3式中b側(cè)澆口的寬度(mm)A塑件的外側(cè)表面積(mm)t側(cè)澆口的厚度(mm)把 A5702+8452+31122=3574 mm代入式中得b1.6 mm b取1.8 mm 則 t=0.6 mm 。澆口是分流道與塑件之間的狹窄部分,。它能使分流道輸送來的熔融塑料的流速產(chǎn)生加速度,形成理想的流態(tài),順序的迅速地充滿型腔,同
- 溫馨提示:
1: 本站所有資源如無特殊說明,都需要本地電腦安裝OFFICE2007和PDF閱讀器。圖紙軟件為CAD,CAXA,PROE,UG,SolidWorks等.壓縮文件請下載最新的WinRAR軟件解壓。
2: 本站的文檔不包含任何第三方提供的附件圖紙等,如果需要附件,請聯(lián)系上傳者。文件的所有權(quán)益歸上傳用戶所有。
3.本站RAR壓縮包中若帶圖紙,網(wǎng)頁內(nèi)容里面會有圖紙預(yù)覽,若沒有圖紙預(yù)覽就沒有圖紙。
4. 未經(jīng)權(quán)益所有人同意不得將文件中的內(nèi)容挪作商業(yè)或盈利用途。
5. 裝配圖網(wǎng)僅提供信息存儲空間,僅對用戶上傳內(nèi)容的表現(xiàn)方式做保護(hù)處理,對用戶上傳分享的文檔內(nèi)容本身不做任何修改或編輯,并不能對任何下載內(nèi)容負(fù)責(zé)。
6. 下載文件中如有侵權(quán)或不適當(dāng)內(nèi)容,請與我們聯(lián)系,我們立即糾正。
7. 本站不保證下載資源的準(zhǔn)確性、安全性和完整性, 同時也不承擔(dān)用戶因使用這些下載資源對自己和他人造成任何形式的傷害或損失。
相關(guān)資源
更多